The fashion industry has evolved dramatically in recent years, driven by both technological innovations and changing consumer expectations. Among the most significant breakthroughs in textile manufacturing is the ultrasonic embossing machine, a powerful tool that enables precise, chemical-free fabric embossing. Particularly in the seamless garment sector, ultrasonic embossing has become a cornerstone technology that allows manufacturers to produce elegant, high-performance apparel without compromising comfort or durability.
In this comprehensive article, we will explore what ultrasonic embossing is, how ultrasonic embossing machines function, their application in seamless garment manufacturing, and why they are becoming an indispensable part of modern textile production.
1. What Is Ultrasonic Embossing?
Ultrasonic embossing is a process that uses high-frequency ultrasonic vibrations to generate localized heat at the interface of two materials. This heat softens or melts synthetic fabrics, enabling them to be reshaped or textured with a patterned roller under pressure.
Unlike traditional thermal or chemical embossing methods, ultrasonic embossing requires no adhesives, glues, or external heat sources. It’s especially effective on synthetic textiles like polyester, nylon, and spandex—materials commonly used in seamless garment manufacturing.
2. How Does an Ultrasonic Embossing Machine Work?
An ultrasonic embossing machine consists of four major components:
Ultrasonic generator: Converts electrical energy into high-frequency signals.
Transducer (converter): Changes the high-frequency electrical signals into mechanical vibrations.
Booster and horn (sonotrode): Amplify and deliver ultrasonic energy to the fabric.
Embossing roller (anvil): Imprints the desired pattern while providing pressure against the sonotrode.
When fabric passes between the vibrating sonotrode and the patterned roller, friction and ultrasonic energy generate heat. This melts the fabric at microscopic points, permanently imprinting the roller’s pattern into the textile. The result is a raised or recessed design that adds both visual appeal and tactile texture.
3. Why Use Ultrasonic Embossing in Seamless Garment Production?
3.1. Enhanced Aesthetic Value
In the seamless garment segment—often focused on sportswear, lingerie, shapewear, and undergarments—design plays a crucial role. Ultrasonic embossing machines can produce detailed logos, lines, or motifs on garments without stitching or screen printing, offering a clean and modern aesthetic.
3.2. Chemical-Free, Eco-Friendly Production
Since ultrasonic embossing doesn’t require solvents, inks, or adhesives, it aligns perfectly with eco-conscious textile production. Many sustainable brands are now embracing this method as part of their green manufacturing strategy.
3.3. Seam Integrity and Comfort
Traditional seams may cause skin irritation or compromise garment stretch. Ultrasonic embossing, on the other hand, is integrated into the fabric itself, eliminating extra layers or threads. This is critical for seamless garments that demand both high elasticity and second-skin comfort.
3.4. Faster Production Cycles
Ultrasonic embossing machines offer high-speed processing capabilities. A single pass through the embossing system can texture meters of fabric in seconds, reducing production time compared to conventional methods.
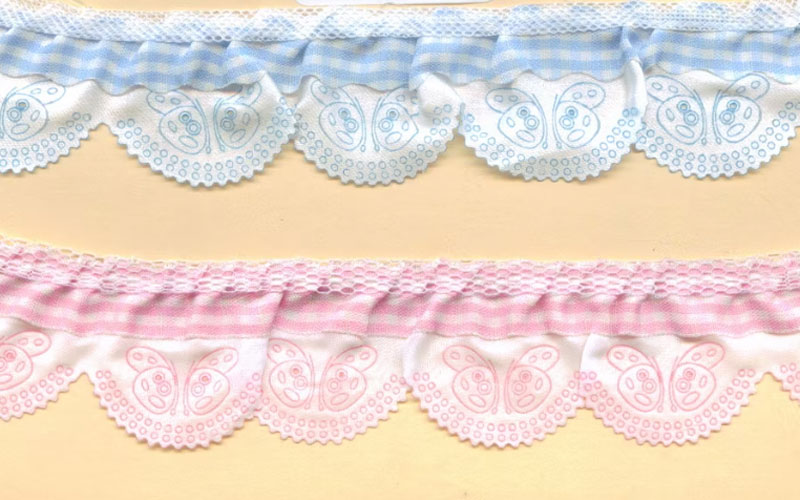
4. Key Features of a High-Quality Ultrasonic Embossing Machine
When choosing an ultrasonic embossing machine for seamless garments, manufacturers should look for the following key specifications:
Feature | Description |
---|---|
Frequency | Typically 20kHz to 35kHz; higher frequencies allow finer detail. |
Roller Width | Adjustable to fabric width—common sizes range from 150mm to 600mm. |
Pattern Design | Customizable rollers allow for logo/text/motif embossing. |
Speed Control | Variable speed settings for optimized fabric feeding. |
Material Compatibility | Must work with polyester, nylon, spandex, and blends. |
Automation | PLC and touchscreen systems for easy operation and precision. |
Many modern machines are also equipped with safety interlocks, cooling systems, and auto-stop features for operator protection and fabric consistency.
5. Ultrasonic Embossing vs. Traditional Embossing: A Comparison
Criteria | Ultrasonic Embossing | Traditional Embossing |
---|---|---|
Heat Source | Ultrasonic vibration | External heating element |
Chemical Use | No | Often uses adhesives/inks |
Energy Efficiency | High | Moderate to low |
Speed | Fast | Slower |
Detail Precision | High | Medium |
Environmental Impact | Low | High |
It is clear from this comparison that ultrasonic embossing is far more suited to modern production needs, especially where sustainability, speed, and precision are key.
6. Application Scenarios in Seamless Garment Manufacturing
6.1. Sportswear and Activewear
Seamless leggings, yoga pants, and running shirts can benefit from ultrasonic embossing by incorporating ventilated textures, brand logos, or ribbing zones for comfort and breathability.
6.2. Lingerie and Intimate Apparel
For delicate garments, especially where visibility and feel are vital, ultrasonic embossing allows subtle decorative effects without irritating seams or bulky embroidery.
6.3. Shapewear
Ultrasonic embossing machines help add compression zones, body-sculpting lines, and visual shaping patterns directly onto seamless shapewear, improving both form and function.
6.4. Medical and Therapeutic Garments
Medical compression garments or therapeutic wear like post-surgical support wear can benefit from embossed indicators, therapeutic pressure zones, or alignment lines.
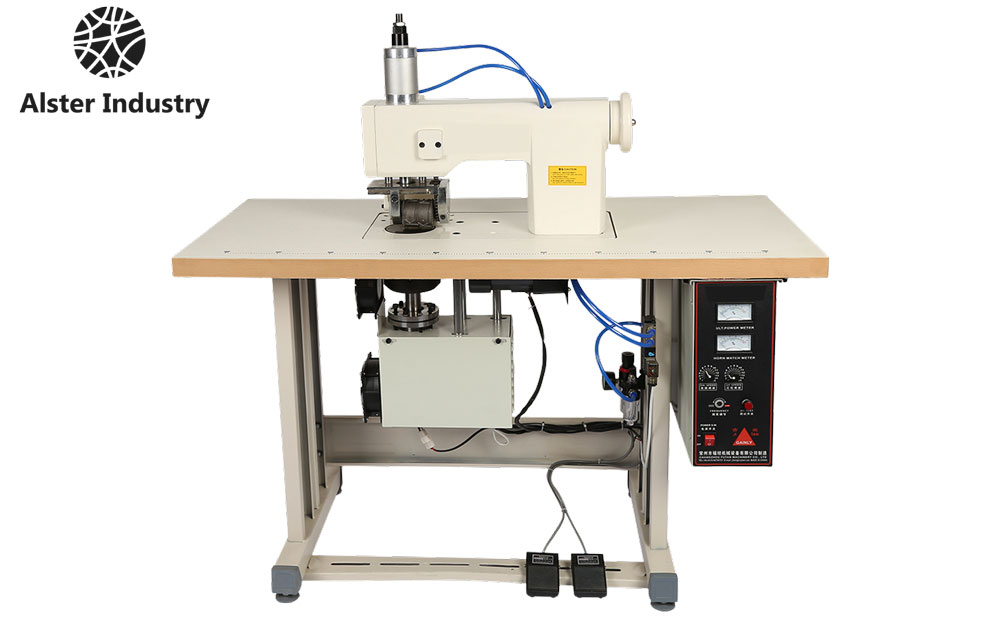
7. Tips for Optimizing Ultrasonic Embossing Machine Use
7.1. Choose the Right Fabric Blend
Although ultrasonic embossing works best on synthetics, fabric composition greatly influences results. A higher polyester content typically leads to sharper patterns.
7.2. Regularly Maintain Rollers and Horns
Worn or dirty rollers and horns can reduce embossing quality or cause inconsistent designs. Regular cleaning and inspection are essential.
7.3. Customize Patterns for Brand Differentiation
Instead of using generic patterns, invest in customized rollers to create brand-specific motifs or designs that enhance product appeal.
7.4. Calibrate Pressure and Speed Settings
Different fabrics require different embossing pressures and speeds. Test before production to determine optimal machine settings.
8. Choosing the Right Ultrasonic Embossing Machine Manufacturer
When investing in ultrasonic embossing machines, it is critical to work with an experienced and specialized manufacturer. Look for suppliers who offer:
Technical training and after-sales service.
Custom pattern roller design services.
Machine testing with your fabric samples.
Long-term parts supply and support.
Choosing a reliable supplier can drastically reduce downtime, increase ROI, and improve embossing consistency.
9. Future Trends in Ultrasonic Embossing for Seamless Garments
9.1. Smart Fabric Integration
Emerging fabrics embedded with conductive threads or smart sensors can be ultrasonically embossed to integrate flexible circuits without disrupting textile integrity.
9.2. 3D Embossing Capabilities
As machine precision improves, 3D-style embossed textures are becoming increasingly viable, adding depth and high-fashion appeal to seamless wear.
9.3. Automation and AI
The integration of AI-powered systems into ultrasonic embossing machines can help automate pattern adjustments, detect errors in real-time, and optimize energy usage.
Conclusion
As seamless garment technology continues to evolve, ultrasonic embossing machines are playing a pivotal role in pushing both design and functionality boundaries. Their precision, eco-friendliness, and efficiency make them an ideal tool for manufacturers looking to stay ahead in the competitive apparel market.
Whether it’s for luxury lingerie, performance-driven activewear, or therapeutic clothing, ultrasonic embossing delivers more than just a visual impact—it creates garments that feel better, perform better, and look undeniably modern.
If you are a textile manufacturer looking to embrace innovation, now is the time to invest in ultrasonic embossing machines from Alster tailored to the seamless garment industry.