In the modern textile and apparel industry, the demand for seamless, durable, and high-quality bonding methods has given rise to the widespread use of hot melt adhesive films. When it comes to bonding strips and lace, which are often used in lingerie, sportswear, fashion garments, and accessories, seamless laminating machines combined with hot melt films offer a highly efficient, threadless, and aesthetically superior solution.
This guide provides a complete overview of how to apply hot melt adhesive films to strips and lace using a seamless laminating machine—from the materials you need to the step-by-step operation and troubleshooting tips for optimal results.
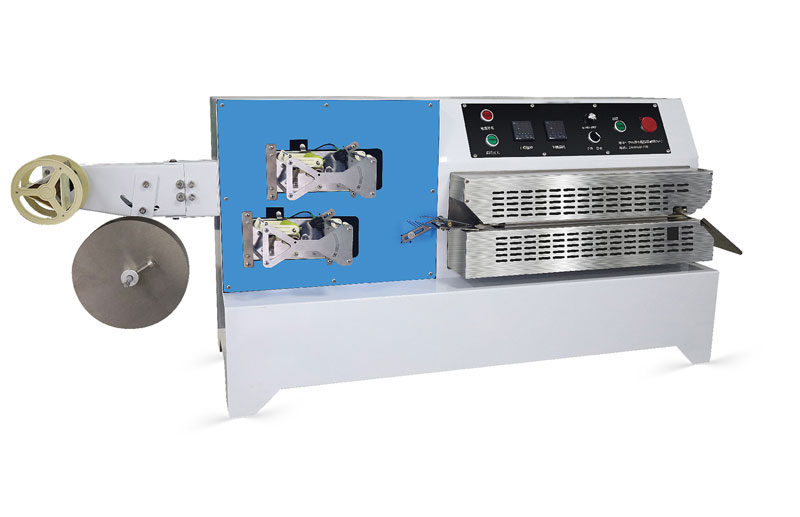
1. Introduction to Hot Melt Adhesive Films and Seamless Lamination
What Are Hot Melt Adhesive Films?
Hot melt adhesive films are thermoplastic films that become tacky upon heating and bond securely upon cooling. They are widely used in textile lamination due to their flexibility, strength, and clean application.
Common types include:
TPU (Thermoplastic Polyurethane): Soft and stretchable; ideal for lace and elastic strips.
PA (Polyamide): Strong, slightly rigid; suited for synthetic fabrics.
PES (Polyester) and EVA: Used for general fabric bonding tasks.
These films are typically supplied in rolls and are applied between layers of fabric using heat and pressure.
Why Use a Seamless Laminating Machine?
Seamless laminating machines offer the ability to bond fabrics without sewing. They use heating rollers and controlled pressure to activate and apply adhesive films. This method is especially useful for intricate fabrics like lace, as it prevents distortion and delivers a clean, flexible bond line.
2. Preparing Materials and Equipment
Before beginning the lamination process, it’s essential to gather and prepare all materials properly to ensure consistent results.
Materials Required:
Strips and lace (pre-cut or in rolls)
Hot melt adhesive film (appropriate for fabric type)
Seamless laminating machine
Cutting tools and templates (optional)
Preparation Checklist:
Fabric Cleaning: Ensure that all materials are free from dust and moisture.
Film Selection: Choose the correct film based on the fabric’s elasticity and thickness.
Film Cutting: Trim the film slightly smaller than the fabric surface to avoid overflow during lamination.
Test Sample: Always test on a small piece of fabric to confirm compatibility and bonding strength.
3. Step-by-Step Lamination Process
Step 1: Machine Setup
Adjust the seamless laminating machine to the correct parameters for the selected film:
Temperature: 110°C to 130°C (for TPU)
Pressure: Medium (2–4 kg/cm²) to protect delicate lace
Speed: Start slow (2–4 m/min) for thin fabrics
Preheat the rollers evenly before loading the materials.
Step 2: Positioning the Layers
Place the adhesive film between the strip and the lace layer.
Align the edges accurately to avoid misalignment during lamination.
Use guiding tools or edge sensors for continuous feeding.
Step 3: Feeding and Bonding
Feed the fabric-film-fabric sandwich into the laminating rollers.
Allow the rollers to apply consistent heat and pressure.
The adhesive film will melt, bond the layers, and then solidify as it cools.
Step 4: Cooling and Finishing
Lay the laminated material on a flat surface to cool completely.
Once cooled, inspect the bond line for even adhesion and strength.
Trim any excess materials if necessary.
4. Troubleshooting and Optimization Tips
Even with the right materials and setup, some issues may occur during lamination. Here’s how to address them:
Issue | Cause | Solution |
---|---|---|
Weak bonding | Low temperature or fast speed | Increase heat or slow down speed |
Adhesive overflow | Film too large | Trim film closer to final fabric size |
Fabric wrinkles or distortion | Excessive pressure or tension | Reduce roller pressure or fabric tension |
Yellowing of lace | Overheating | Lower the temperature slightly |
Adhesive not melted properly | Short heating time | Reduce speed or increase temperature |
For consistent production quality, document machine settings for each material type used.
5. Applications in the Textile Industry
The bonding of lace and strips using hot melt adhesive films is applied across various sectors:
Lingerie and Intimate Apparel
Delicate lace materials are laminated to elastic bands without stitching, providing comfort and an elegant finish for bras, panties, and shapewear.
Sportswear and Performance Apparel
Elastic strips are laminated for waistbands, cuffs, or seams to maintain stretch while reducing skin irritation from stitches.
Fashion Accessories
Lace or decorative strips are seamlessly bonded to handbags, scarves, or shoes for a clean design aesthetic.
Medical Textiles
Hot melt films are used to bond strips on wraps, compression wear, and wearable medical devices due to their skin-friendly and solvent-free properties.
6. Maintenance and Best Practices
To ensure the longevity and performance of your seamless laminating machine:
Clean rollers regularly: Prevent adhesive buildup which can damage fabric or cause uneven lamination.
Monitor roller temperature: Use infrared sensors or built-in displays.
Check pressure calibration: Over time, rollers may need adjustment to maintain correct pressure levels.
Replace worn parts: Keep an inventory of belts, motors, and rollers for quick maintenance.
Additionally, store hot melt adhesive films in a cool, dry place and avoid exposure to humidity, which can affect their bonding performance.
Conclusion
Using hot melt adhesive films with a seamless laminating machine is an advanced and efficient method to bond lace and strips in the textile industry. With the right setup, materials, and technique, manufacturers can achieve clean, flexible, and highly durable results that elevate both the quality and comfort of final garments or accessories.
This process not only enhances aesthetic appeal but also supports high-volume production with minimal waste, reduced labor, and consistent quality—making it an ideal solution for modern, eco-conscious textile production.