In today’s fast-paced textile and garment manufacturing industry, achieving clean, precise, and efficient fabric cutting is more critical than ever. Traditional cutting methods often lead to fraying, uneven edges, and material distortion, especially with synthetic fabrics. To meet the growing demands for quality and efficiency, many manufacturers are turning to the ultrasonic cutting machine for fabric — a cutting-edge solution transforming how fabrics are processed.
In this comprehensive blog post, we explore how ultrasonic cutting technology works, its advantages, applications, and why it’s becoming a staple in modern textile production.
What Is an Ultrasonic Cutting Machine for Fabric?
An ultrasonic cutting machine for fabric uses high-frequency ultrasonic vibrations to slice through materials with exceptional precision. Unlike mechanical cutting tools, ultrasonic cutters do not rely on sharp blades. Instead, they employ a vibrating horn or sonotrode that transmits ultrasonic waves (usually at 20–40 kHz) to the fabric. These vibrations generate localized heat due to molecular friction, allowing the material to be separated cleanly with minimal resistance.
This process is particularly effective for synthetic fabrics, such as polyester, nylon, and non-wovens, where the generated heat seals the edges during cutting — preventing fraying and eliminating the need for additional edge-finishing steps.
How Ultrasonic Cutting Technology Works
Ultrasonic cutting is based on a principle called piezoelectric effect, where ceramic transducers convert electrical energy into mechanical vibrations. Here’s a simplified breakdown of how an ultrasonic cutting machine for fabric operates:
Power Generation
The ultrasonic generator converts standard electrical current into high-frequency electrical signals.Transducer Activation
The electrical signals activate piezoelectric ceramics in the transducer, generating mechanical vibrations.Sonotrode Vibration
These vibrations are transmitted through the sonotrode (horn), which oscillates at high frequency.Fabric Separation
When the vibrating horn contacts the fabric, it generates heat through internal molecular friction, allowing the material to be “melt-cut” cleanly.
This friction-based, blade-less cutting system is contactless in many cases, reducing material distortion and wear on tools.
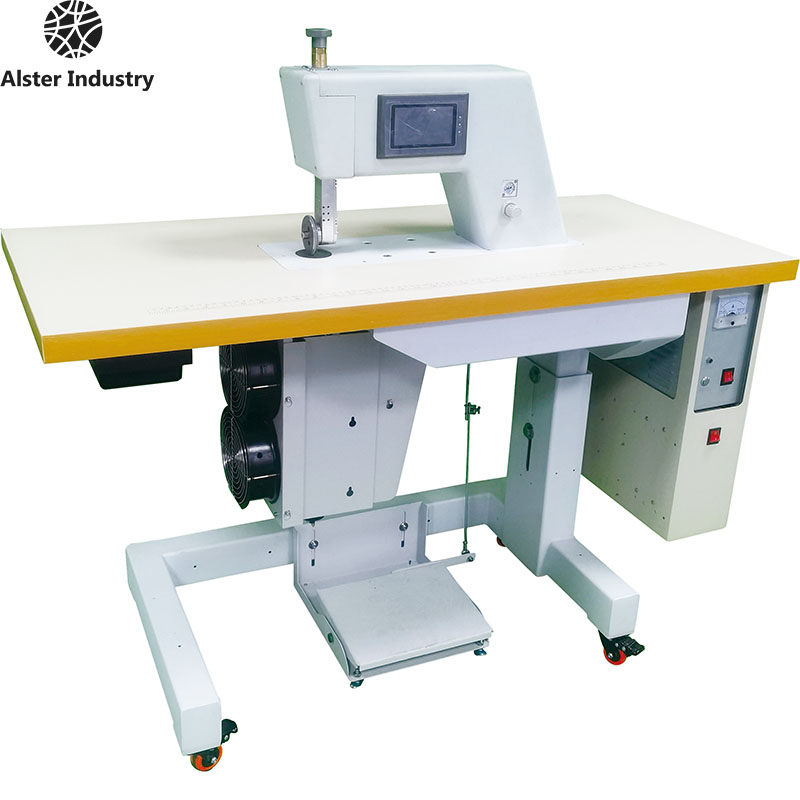
Advantages of Ultrasonic Cutting Machine for Fabric
Switching to an ultrasonic cutting machine for fabric offers numerous benefits for textile manufacturers. Some of the most significant include:
1. Clean and Sealed Edges
The ultrasonic energy melts and seals synthetic fabric edges during cutting, eliminating fraying and reducing the need for secondary processing.
2. High Cutting Precision
Ultrasonic cutting provides consistent and highly accurate cuts, which is crucial in applications requiring precision like apparel panels, labels, or technical textiles.
3. No Blade Contamination
Unlike mechanical cutters, ultrasonic cutting tools do not suffer from residue buildup, especially when working with sticky or laminated fabrics.
4. Reduced Maintenance
Since there is no sharp blade to dull or replace regularly, maintenance costs are significantly lower over time.
5. Fast and Efficient
Ultrasonic cutters work at high speed and are ideal for continuous cutting operations in production lines, boosting overall productivity.
6. Versatile Applications
From delicate lace to dense non-woven filters, the ultrasonic cutting machine handles a wide range of materials without distortion.
Applications of Ultrasonic Cutting Machine in the Textile Industry
The versatility and efficiency of the ultrasonic cutting machine for fabric have led to its widespread adoption across numerous sectors. Some key application areas include:
1. Garment Manufacturing
Ultrasonic cutting is ideal for trimming synthetic fabric patterns, collars, cuffs, and decorative panels without leaving loose threads.
2. Label and Tag Cutting
Woven and printed labels made of polyester or acetate are cleanly cut without fraying, making ultrasonic cutting indispensable in label production.
3. Nonwoven and Technical Textiles
In hygiene products, filtration materials, and medical textiles, ultrasonic cutting enables clean edges without contamination or fiber loss.
4. Automotive Interiors
Car seat fabrics, headliners, and interior linings require precise cuts. Ultrasonic technology delivers this with speed and repeatability.
5. Home Textiles
For items like curtains, upholstery, and decorative items, ultrasonic cutting ensures straight, sealed lines that improve product durability and finish.
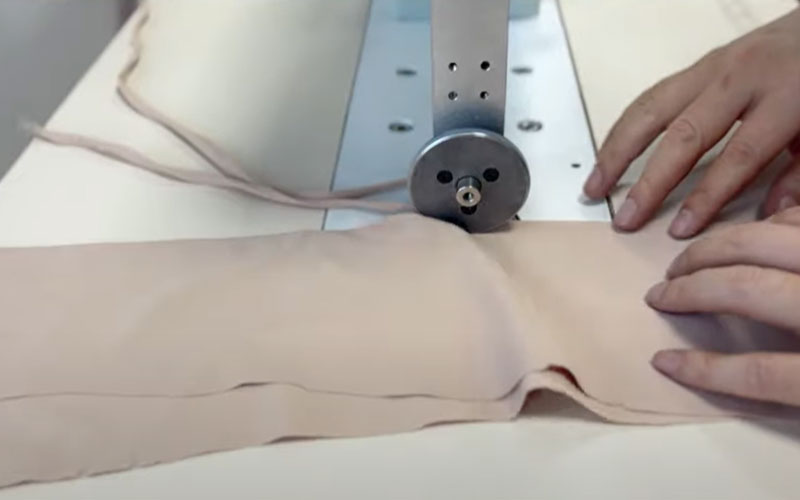
Key Features to Consider When Choosing an Ultrasonic Cutting Machine
When selecting an ultrasonic cutting machine for fabric, manufacturers must consider several technical and operational factors:
1. Frequency and Power Output
Standard ultrasonic frequencies range from 20 kHz to 40 kHz. Higher frequencies are ideal for fine materials, while lower frequencies suit thicker fabrics.
2. Cutting Speed
Machines with adjustable speed settings allow greater control for different materials and pattern complexities.
3. Type of Cutter Head
Rotary blades, guillotine-style sonotrodes, or hand-held wands each suit different production environments. Choose based on your application needs.
4. Integration Options
Look for machines that can be integrated into existing production lines or CNC systems for automated operations.
5. Material Compatibility
Ensure the machine is compatible with the types of fabrics you use — especially if you’re working with composite or laminated materials.
6. Operator Safety and Ergonomics
Safety guards, user-friendly interfaces, and ergonomic designs improve operator experience and minimize workplace hazards.
Comparing Ultrasonic Cutting vs. Traditional Cutting Methods
Let’s briefly compare ultrasonic cutting machines for fabric with more traditional cutting methods:
Cutting Method | Edge Finish | Maintenance | Speed | Ideal For |
---|---|---|---|---|
Manual Scissors | Frayed edges | High (blades dull) | Slow | Small-scale, artisan |
Die Cutting | Good (depends on die) | Medium | Medium | High-volume, basic shapes |
Laser Cutting | Clean (burn marks possible) | Medium | Fast | Synthetics, complex shapes |
Ultrasonic Cutting | Clean, sealed | Low | Very fast | Wide range of fabrics |
Ultrasonic cutting clearly stands out when it comes to clean finish, speed, and low maintenance.
Common Fabrics Compatible with Ultrasonic Cutting
The ultrasonic method is especially suitable for thermoplastic or synthetic fabrics, including:
Polyester
Nylon
Acetate
Polypropylene
Acrylic
Viscose blends
Nonwoven fabrics
Polyamide
Natural fibers like cotton or wool do not melt and therefore are less suited to ultrasonic cutting — although blends containing synthetic fibers can still benefit.
Challenges and Limitations of Ultrasonic Fabric Cutting
While the ultrasonic cutting machine for fabric offers many advantages, it’s important to recognize a few limitations:
Material Compatibility: Pure natural fibers may not yield clean cuts since they do not melt.
Initial Investment: Ultrasonic machines tend to be more expensive upfront than mechanical cutters.
Heat Sensitivity: Overheating thin or delicate materials may cause discoloration or melting defects.
Operator Training: Proper training is essential to use the machine safely and efficiently.
These challenges can be mitigated with proper machine calibration, operator education, and thoughtful material selection.
Trends and Innovations in Ultrasonic Fabric Cutting
The global textile industry is witnessing increasing demand for eco-friendly, fast, and high-precision solutions. This has led to several innovations in ultrasonic fabric cutting:
Integration with Robotics: Robotic arms equipped with ultrasonic cutters are being used in automated sewing and cutting lines.
Smart Cutting Systems: AI-driven systems can adjust cutting parameters in real time based on material type and thickness.
Portable Ultrasonic Tools: Handheld ultrasonic cutters are gaining popularity for small-scale, on-demand production needs.
Energy Efficiency Improvements: Newer machines are more energy-efficient, reducing power consumption per unit cut.
These trends further enhance the appeal of the ultrasonic cutting machine for fabric in modern manufacturing.
Final Thoughts: Is an Ultrasonic Cutting Machine Right for You?
If your textile production involves synthetic or blended fabrics and requires high-precision, sealed-edge cutting at scale, investing in an ultrasonic cutting machine for fabric is likely a smart move. The combination of efficiency, reduced maintenance, and edge quality far outweighs the initial investment — especially for businesses looking to scale or automate their operations.
At Alster, we specialize in manufacturing high-performance ultrasonic cutting machines for fabric, designed to meet the rigorous demands of the textile industry. Whether you’re looking for compact units for small batches or automated solutions for mass production, we offer a range of customizable options to fit your needs.
Ready to enhance your textile cutting process?
Contact Alster today to learn more about our ultrasonic fabric cutting solutions and get expert advice on choosing the right model for your operations.