In today’s fast-paced manufacturing and packaging industries, the demand for high-performance bonding solutions continues to grow. Among the most reliable and versatile bonding agents are hot melt adhesives. These thermoplastic materials, applied in a molten state and solidified upon cooling, offer rapid bonding, minimal waste, and efficient performance across diverse applications. As industries push toward faster production cycles, automation, and eco-friendly alternatives, hot melt adhesive manufacturers are playing a pivotal role in shaping the future of modern manufacturing.
This article offers a comprehensive look into the landscape of hot melt adhesive production. We’ll explore the technologies behind these adhesives, the types available, their applications across various industries, how to evaluate quality suppliers, and what differentiates leading hot melt adhesive manufacturers from others in the global market.
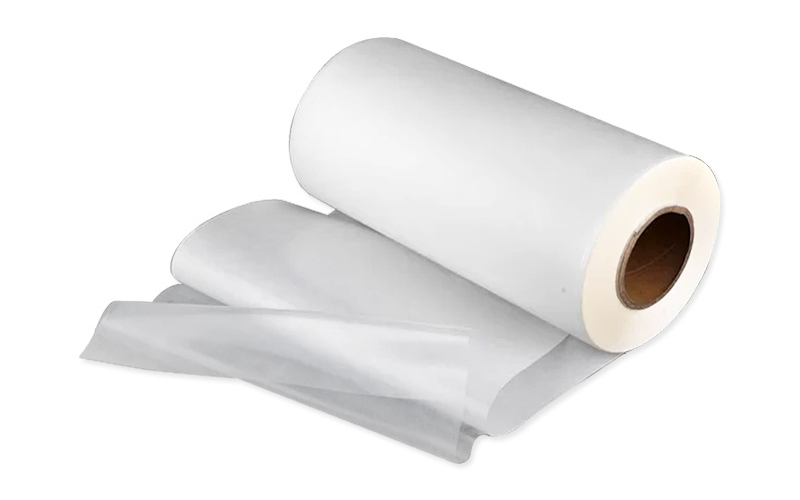
1. What Is Hot Melt Adhesive?
Hot melt adhesive (HMA) is a form of thermoplastic adhesive that is applied in a molten state and hardens upon cooling, forming a strong bond. Unlike solvent-based adhesives, HMAs contain no water or solvents, allowing for faster setting and curing times. This makes them ideal for applications where speed and efficiency are crucial, such as packaging, product assembly, woodworking, textile bonding, electronics, and automotive interior applications.
Key Features of Hot Melt Adhesives:
Fast setting time – improves throughput and automation efficiency.
Solvent-free formulation – safer for operators and the environment.
High bond strength – suitable for various materials like plastic, wood, fabric, and metal.
Clean processing – minimal residue, easy to handle, and low waste.
Versatile formats – available as pellets, sticks, blocks, and even films.
Because of these properties, the demand for hot melt adhesives continues to expand globally, prompting innovation from hot melt adhesive manufacturers around the world.
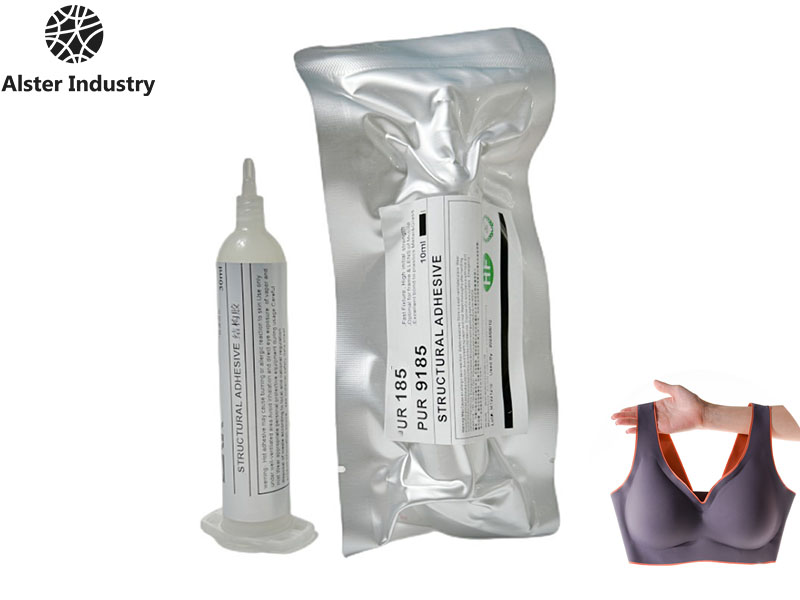
2. Types of Hot Melt Adhesives
Understanding the types of hot melt adhesives available helps end-users select the best product for their needs. Below are the major categories:
a) EVA-Based Hot Melt Adhesive
Ethylene-vinyl acetate (EVA) is the most commonly used base polymer in traditional hot melt adhesives. These are typically used in packaging, bookbinding, and paper lamination due to their good adhesion to porous surfaces.
b) Polyolefin Hot Melt
This type offers superior resistance to oxidation and high temperatures. Polyolefin-based HMAs are ideal for hygiene products, filtration systems, and some electronics.
c) Polyamide Hot Melt Adhesive
Polyamide adhesives offer excellent chemical and oil resistance and are suitable for automotive, electrical, and textile applications.
d) Polyurethane Reactive (PUR) Hot Melt
PUR adhesives react with ambient moisture after application to form a thermoset bond. They provide stronger, more heat- and moisture-resistant bonds than traditional hot melts, commonly used in woodworking and complex plastic bonding.
e) Pressure-Sensitive Hot Melt Adhesives (PSA)
These remain tacky even after solidifying and are used in tapes, labels, and hygiene products.
Each of these types has specific manufacturing requirements and performance profiles, making it essential for hot melt adhesive manufacturers to specialize and refine their formulations for targeted markets.
3. What Are Hot Melt Adhesive Films?
In addition to pellets and sticks, hot melt adhesives are also available in film format. Hot melt adhesive films are thin, flexible sheets that provide uniform thickness and easy handling. They are activated by heat and pressure, making them ideal for automated production lines.
Advantages of Hot Melt Adhesive Films:
Consistent thickness and quality
Low VOC emissions
Simplified application process
Excellent bonding strength
Clean aesthetic with no oozing or stringing
Applications include textiles, automotive interiors, footwear, electronics assembly, and composite bonding. Manufacturers are increasingly investing in film production to meet industry demands for precision and sustainability.
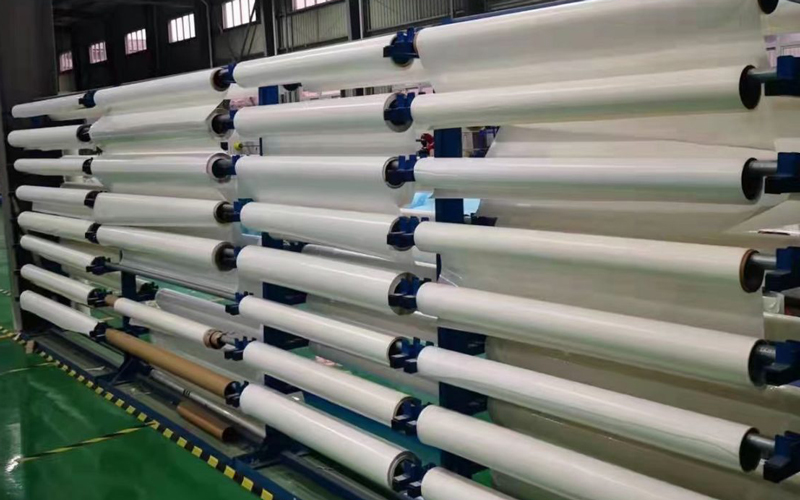
4. Industries Served by Hot Melt Adhesive Manufacturers
Hot melt adhesives serve nearly every industrial sector thanks to their fast bonding, adaptability, and cost-effectiveness. Let’s look at some key industries:
Packaging Industry
HMAs are widely used in case and carton sealing, label applications, and paper lamination. Their rapid setting ability allows for fast-moving production lines without compromising bond integrity.
Automotive Industry
From door panel lamination to acoustic insulation and wiring harness protection, hot melt adhesives provide vibration resistance, durability, and reduced assembly time.
Footwear & Textile
Hot melt adhesive films are used in bonding leather, fabric, and technical textiles, offering a lightweight, flexible alternative to sewing or stitching.
Electronics
Miniaturization and precise assembly demand adhesives with clean processing, thermal resistance, and insulation properties.
Furniture & Woodworking
PUR-based HMAs provide strong, moisture-resistant bonds for furniture edge banding, laminate bonding, and profile wrapping.
Medical & Hygiene Products
PSAs in diapers, sanitary napkins, and surgical drapes offer comfort, hygiene, and performance without skin irritation.
For hot melt adhesive manufacturers, customization and consistent quality are essential to serve such diverse markets effectively.
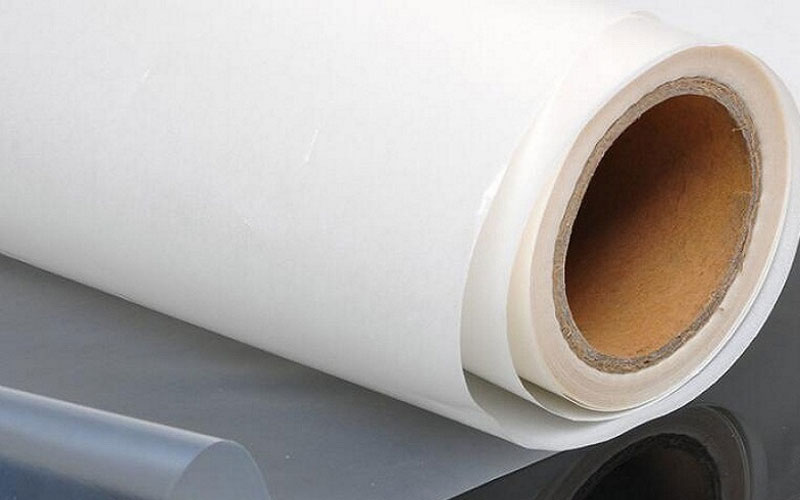
5. What to Look for in a Hot Melt Adhesive Manufacturer
Choosing the right hot melt adhesive manufacturer is critical to ensuring product performance, reliability, and regulatory compliance. Below are key factors to consider:
1. Product Range and Customization
A quality manufacturer should offer a wide range of adhesives tailored for various substrates and conditions. Custom formulations for niche applications are a strong advantage.
2. Manufacturing Capabilities
Advanced equipment, R&D labs, and clean production environments are signs of a reliable producer. Look for manufacturers who have scalable production and can meet large or urgent orders.
3. Quality Control and Certifications
ISO certification, REACH and RoHS compliance, and in-house testing capabilities are essential indicators of quality and safety.
4. Technical Support and Application Expertise
Good manufacturers don’t just sell products—they offer technical training, troubleshooting support, and ongoing consultation to ensure proper use of their adhesives.
5. Sustainability Initiatives
As environmental regulations tighten, many hot melt adhesive manufacturers are developing bio-based, recyclable, and energy-efficient products. Partnering with such producers positions your business for future compliance and ESG goals.
6. The Role of Innovation in the Hot Melt Adhesive Industry
The global adhesive industry is being reshaped by innovation and sustainability trends. Manufacturers are investing in:
Bio-based adhesives made from renewable sources
Low-temperature hot melts that save energy and reduce substrate damage
Smart adhesives that change properties under specific conditions (e.g., heat-activated labels)
Advanced polymer blends offering improved flexibility, heat resistance, and adhesion to difficult substrates
Leading hot melt adhesive manufacturers are also integrating automation, AI-driven quality control, and digital inventory tracking into their production and logistics systems, ensuring better service to OEMs and industrial users.
7. Overview of the Global Market for Hot Melt Adhesives
The global hot melt adhesives market is projected to reach over USD 11 billion by 2030, driven by growth in e-commerce packaging, construction, automotive lightweighting, and consumer electronics.
Asia-Pacific leads the market share due to its massive manufacturing base, while North America and Europe are investing heavily in sustainable adhesives and high-performance formulations. The demand for hot melt adhesive films is growing particularly fast in automotive, footwear, and textiles.
This growing demand creates both opportunities and challenges for hot melt adhesive manufacturers, who must balance scale, customization, and sustainability.
8. Spotlight: Alster – A Quality Hot Melt Adhesive Manufacturer in China
Among the numerous hot melt adhesive manufacturers in the Asia-Pacific region, Alster has gained attention for its commitment to quality and innovation. Based in China, Alster specializes in producing hot melt adhesive films and rolls tailored for the textile, automotive, and packaging industries.
With a strong R&D team and a focus on customized solutions, Alster supports global customers with high-performance adhesives that meet stringent international standards. While not the only producer in the space, Alster’s focus on innovation and responsive service makes it a brand worth considering for industrial buyers.
9. Challenges Faced by Hot Melt Adhesive Manufacturers
Despite their advantages, manufacturers face several challenges:
Raw Material Volatility: Many HMAs rely on petroleum-based ingredients. Fluctuations in resin prices can affect margins and pricing strategies.
Customization Pressure: With clients demanding unique adhesives, manufacturers must invest in R&D and maintain flexibility in production.
Environmental Regulations: As countries adopt stricter VOC and plastic use laws, adhesive producers must innovate rapidly to remain compliant.
Supply Chain Disruptions: Delays in logistics or raw material shortages can significantly impact production schedules.
Forward-thinking hot melt adhesive manufacturers must invest in resilient sourcing, advanced testing, and lean production models to remain competitive.
10. Final Thoughts: Why Partnering with the Right Hot Melt Adhesive Manufacturer Matters
In an increasingly competitive and fast-evolving industrial landscape, adhesives are not just a component—they are a performance differentiator. Whether you’re sealing boxes, assembling electronics, or bonding textiles, choosing the right hot melt adhesive impacts your product quality, processing speed, and bottom line.
As a procurement officer, engineer, or business owner, working with experienced, innovative, and reliable hot melt adhesive manufacturers ensures long-term value. By focusing on consistency, technical support, and sustainability, these manufacturers enable your operations to stay ahead of industry demands.
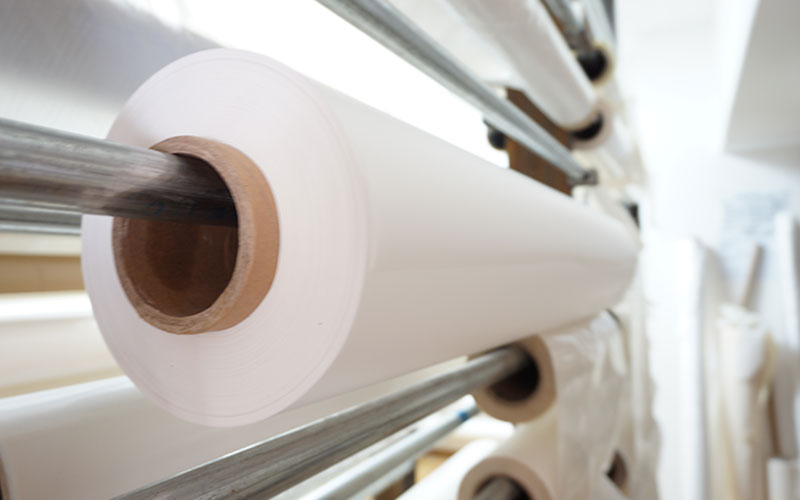
Summary
Hot melt adhesives are thermoplastic bonding agents used across numerous industries for their fast setting, versatility, and strength.
Common types include EVA, polyolefin, PUR, and hot melt films.
Hot melt adhesive films are gaining popularity for their clean processing and consistent thickness.
Key application industries include packaging, automotive, textiles, electronics, and furniture.
Selecting the right hot melt adhesive manufacturer depends on product range, technical support, customization, and sustainability.
Innovation and green chemistry are shaping the future of adhesive manufacturing.
Alster is one example of a quality Chinese manufacturer offering reliable hot melt adhesive solutions.
Partnering with reputable manufacturers ensures long-term production success and regulatory compliance.
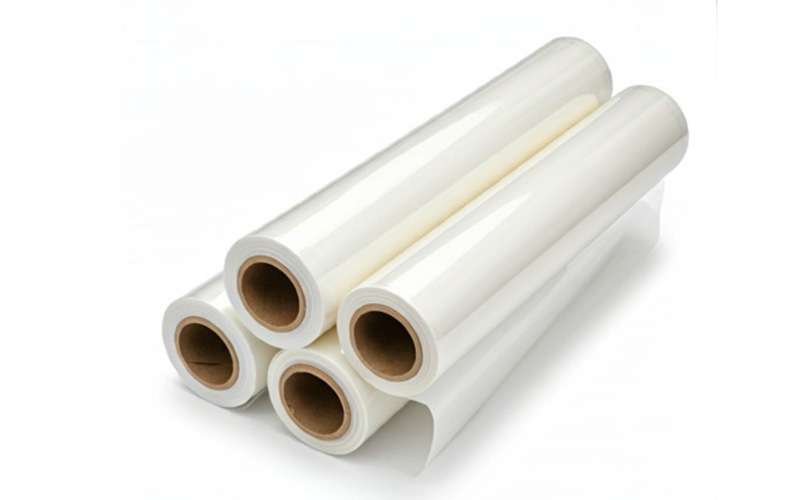
Conclusion
Selecting the right hot melt film manufacturers is critical for your product’s success. By understanding the types of hot melt films, industry trends, manufacturing processes, and evaluating suppliers carefully, you can ensure you get the best quality adhesive films at competitive prices.
Remember, the ideal manufacturer offers a balance of product quality, technical expertise, reliable delivery, and cost efficiency. Whether you operate in packaging, automotive, textile, or electronics, investing time in choosing the right hot melt film partner will pay dividends in product performance and customer satisfaction.