In today’s advanced manufacturing industries, finding reliable, clean, and efficient bonding solutions is critical. One innovative adhesive product that continues to gain popularity across various sectors is the thermoplastic adhesive film. Unlike traditional adhesives that often require solvents, extended curing times, or mechanical fasteners, thermoplastic adhesive films offer a simple, solvent-free, and highly efficient solution.
But what exactly is a thermoplastic adhesive film? What is the difference between thermoplastic adhesive film and hot melt adhesive film? What makes it so effective, and why are industries like textiles, automotive, aerospace, and electronics turning to this technology? This article dives deep into the characteristics, applications, benefits, and key considerations related to thermoplastic adhesive films.
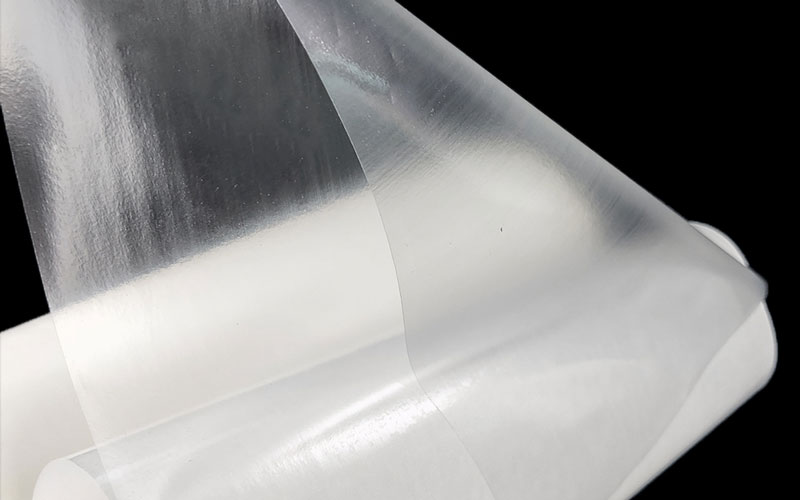
What is Thermoplastic Adhesive Film?
Thermoplastic adhesive film is a solid, solvent-free adhesive material that becomes tacky or flowable when heated, allowing it to bond materials together. Upon cooling, it solidifies to form a strong bond. As the name suggests, it is composed of thermoplastic polymers, which means it can be reheated and re-melted multiple times without undergoing chemical change.
These films are generally supplied in rolls or sheets and are used in lamination or multilayer bonding processes. They are available in a wide variety of formulations and thicknesses to meet different bonding requirements.
Key Characteristics of Thermoplastic Adhesive Film
Heat-Activated
The film remains inactive at room temperature but becomes adhesive when exposed to specific heat and pressure conditions.Reversible Bonding
Since it is thermoplastic, the bond is reversible upon reheating, allowing for repositioning or rework in many cases.No Solvent or VOCs
Unlike liquid adhesives, thermoplastic adhesive films are solid and do not emit volatile organic compounds (VOCs), making them environmentally friendly and safer to handle.Excellent Handling
These films are clean to apply, non-tacky in their inactive state, and easy to cut, store, and transport.Variety of Base Polymers
Common materials include EVA (Ethylene Vinyl Acetate), TPU (Thermoplastic Polyurethane), PA (Polyamide), PES (Polyester), and others.
Common Applications of Thermoplastic Adhesive Film
The use of thermoplastic adhesive film spans numerous industries due to its versatile bonding properties and compatibility with various substrates. Here are some common application areas:
1. Textile and Apparel Industry
Used for seam sealing, heat transfer labels, decorative films, and fabric lamination.
TPU-based adhesive films are favored for their softness and elasticity.
2. Automotive
Applied in interior lamination, sound-deadening materials, door panels, and airbags.
Offers strong adhesion to metal, fabric, and plastic components.
3. Electronics
Enables precise bonding of flexible circuits, heat spreaders, and display panels.
Provides thermal and dielectric insulation.
4. Footwear
Used to bond different layers of soles and upper materials.
Maintains flexibility and durability even under stress.
5. Medical Industry
For bonding wearable medical sensors, nonwoven fabrics, and breathable membranes.
Non-toxic and biocompatible grades are available.
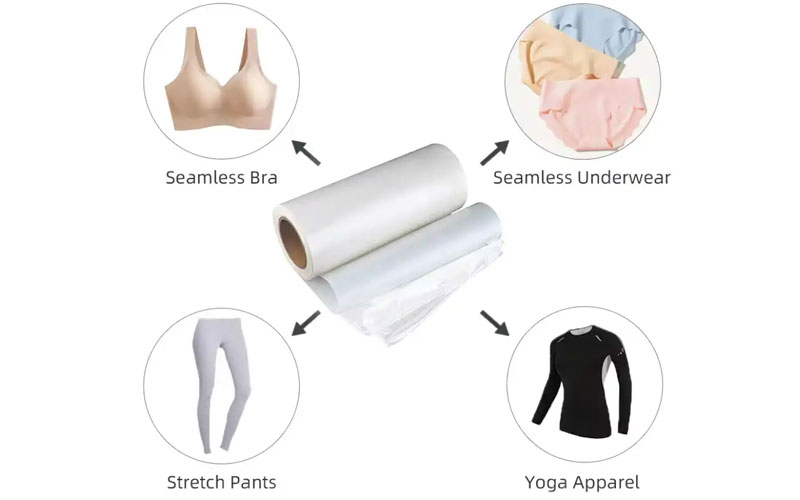
Advantages of Thermoplastic Adhesive Film
There are many reasons manufacturers prefer thermoplastic adhesive film over traditional adhesive methods:
✅ 1. Clean and Easy Processing
No dripping, no overspray, and no sticky mess. Thermoplastic films allow for precision placement, reducing material waste and cleanup time.
✅ 2. Improved Workplace Safety
Since there are no solvents, the films eliminate harmful VOC emissions, improving air quality and making them compliant with strict environmental regulations.
✅ 3. Enhanced Bond Performance
Thermoplastic films offer strong adhesion, excellent chemical resistance, and durability across a wide temperature range. This ensures long-lasting performance even in harsh environments.
✅ 4. Automation Friendly
The film format is compatible with automated lamination machines, enabling fast, scalable, and repeatable production workflows.
✅ 5. Customization
Manufacturers can tailor the film thickness, melting point, and adhesion properties based on the application, allowing for more flexibility in design and function.
Types of Thermoplastic Adhesive Films
There are several types of thermoplastic adhesive films, depending on their base polymer:
Type | Melting Point | Key Features | Applications |
---|---|---|---|
EVA | 60–80°C | Flexible, economical | Textiles, footwear, packaging |
TPU | 90–130°C | Elastic, breathable | Sportswear, medical, automotive |
PA (Nylon) | 100–150°C | High bond strength | Automotive, composites |
PES | 120–160°C | High temperature resistance | Electronics, aerospace |
Each type offers unique mechanical and thermal properties, making it important to select the right film based on substrate compatibility and application conditions.
Thermoplastic Adhesive Film vs Hot Melt Adhesive Film
While these terms are often used interchangeably, it’s important to understand the nuance:
Thermoplastic adhesive film refers broadly to any film made from thermoplastic resins used for bonding.
Hot melt adhesive film is a subcategory that specifically refers to thermoplastic films that are activated using heat and pressure, commonly used in high-volume industrial bonding.
So while all hot melt adhesive films are thermoplastic, not all thermoplastic adhesive films are necessarily hot melt formulations. Some may be designed for bonding under different processing conditions.
Choosing the Right Thermoplastic Adhesive Film
When selecting a thermoplastic adhesive film for your application, consider the following factors:
Substrate Compatibility
Ensure the film adheres well to the materials you’re bonding (e.g., metal, fabric, plastic).Processing Temperature
Match the film’s activation temperature to your existing processing equipment.Bond Strength and Durability
Evaluate whether the bond needs to withstand stress, moisture, chemicals, or heat.Film Thickness
Thinner films are suitable for delicate applications, while thicker ones offer stronger adhesion for structural parts.Elasticity and Flexibility
For flexible substrates or wearable applications, select films with a soft, elastic base like TPU.
Future Trends in Thermoplastic Adhesive Films
With sustainability and high-performance materials in demand, the thermoplastic adhesive film market is evolving:
Bio-based polymers are emerging as eco-friendly alternatives.
Smart adhesive films with added functionalities like thermal conductivity, electrical insulation, or shape memory are gaining attention.
Recyclable multilayer bonding using compatible thermoplastic layers is being developed to support circular manufacturing.
The future of thermoplastic adhesive film is set to expand with innovations in polymer science and automation technology.
Conclusion
To summarize, thermoplastic adhesive film is a versatile, efficient, and eco-friendly bonding solution with wide applications across industries. Its heat-activated, solvent-free nature offers significant advantages over traditional adhesives, including better cleanliness, safer handling, and automation compatibility.
As industries continue to demand stronger, more efficient, and sustainable bonding methods, the adoption of thermoplastic adhesive films is expected to grow. Whether you’re in textiles, automotive, electronics, or medical devices, there’s likely a thermoplastic adhesive film formulation tailored to your needs.