As industries continue to evolve towards higher efficiency and sustainability, adhesive technologies have followed suit. Among various thermoplastic bonding solutions, polyamide based hot melt adhesives have gained significant attention for their high performance, versatility, and environmental compatibility.
From electronics to textiles, automotive to packaging, these adhesives play an increasingly critical role in ensuring strong, durable, and heat-resistant bonds. But what is polyamide based hot melt adhesives, and why are they being widely adopted across industries?
In this in-depth SEO blog article, we will explore everything you need to know about polyamide based hot melt adhesives, including their chemistry, performance benefits, forms such as adhesive film, typical applications, and future development trends.
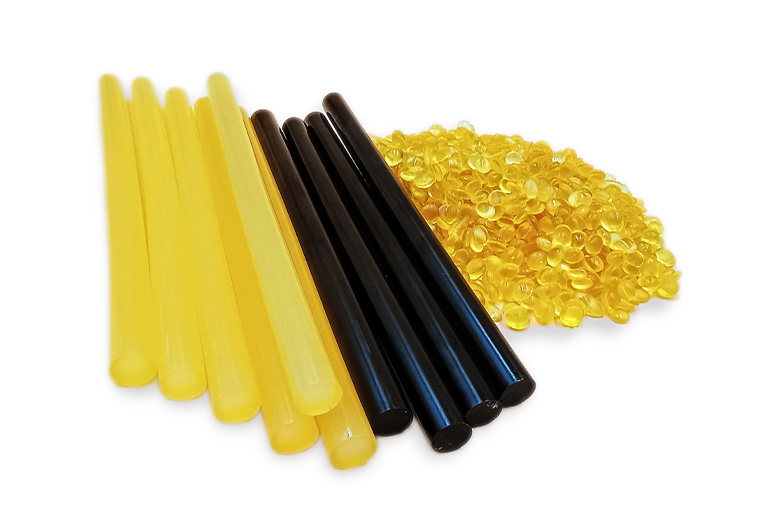
1. What is Polyamide Based Hot Melt Adhesives?
Polyamide based hot melt adhesives are thermoplastic bonding materials derived from polyamide polymers. Unlike traditional solvent-based adhesives, hot melt adhesives do not require water or solvents to cure or dry. They solidify upon cooling, forming a strong bond between substrates.
Polyamide is a synthetic polymer with excellent thermal and chemical resistance. When used in hot melt adhesives, polyamide provides high adhesion strength, flexibility, and durability—even under high heat or harsh environmental conditions.
These adhesives come in several forms, including:
Granules or pellets (for melting in extrusion or spray systems)
Films (for lamination and seamless garment bonding)
Powders (for dot coating or transfer printing)
Among them, polyamide based hot melt adhesive film is becoming particularly popular for precise and solvent-free lamination in high-end applications like technical textiles and electronics.
2. Chemical Structure of Polyamide Based Hot Melt Adhesives
Polyamide polymers are made from diamines and diacids through a condensation reaction. The resulting structure includes recurring amide linkages (-CONH-) in the main polymer chain. This structure grants polyamides their distinct physical properties:
High melting points
Strong hydrogen bonding between polymer chains
Excellent resistance to oils, solvents, and abrasion
These attributes are passed on to polyamide based hot melt adhesives, making them ideal for demanding industrial bonding needs.
There are two major types of polyamide hot melts:
Type | Description | Application |
---|---|---|
Reactive Polyamide (RPA) | Crosslinks after application, offering stronger chemical resistance | Automotive, aerospace |
Non-reactive Polyamide (NRPA) | Thermoplastic and reversible bonding | Textiles, electronics, packaging |
3. Advantages of Polyamide Based Hot Melt Adhesives
Why are manufacturers increasingly turning to polyamide based hot melt adhesives over other adhesive systems?
3.1. High Heat Resistance
These adhesives can maintain structural integrity at elevated temperatures, with some grades resistant to temperatures above 160°C. This makes them ideal for electronics, automotive under-the-hood components, and industrial filters.
3.2. Superior Chemical Resistance
Polyamide adhesives resist oils, solvents, plasticizers, and greases—unlike EVA or polyester-based adhesives. This expands their use to demanding chemical environments.
3.3. Excellent Bond Strength
Whether bonding metal to fabric or plastic to rubber, polyamide based hot melt adhesives offer strong initial tack and long-term durability.
3.4. Flexibility and Toughness
Polyamide adhesives remain flexible even after solidification. This is essential for applications where vibration, bending, or dynamic stress is common.
3.5. Fast Processing & No Curing Time
Like all hot melt adhesives, polyamide types bond quickly without the need for drying or curing, accelerating production cycles.
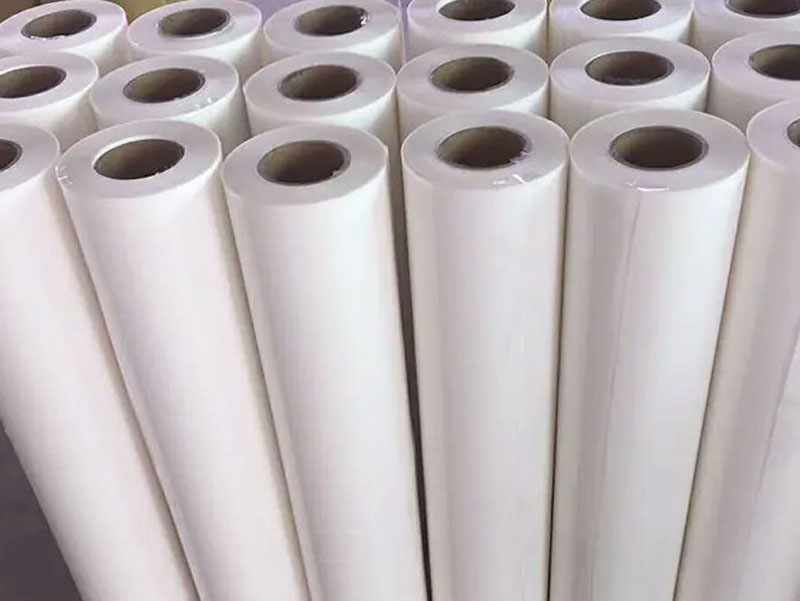
4. Applications of Polyamide Based Hot Melt Adhesives
4.1. Seamless Garment Manufacturing
One of the most innovative applications of polyamide based hot melt adhesive film is in the seamless garment industry. Used for bonding panels in bras, underwear, and sportswear, the adhesive provides:
Strong, flexible bonds
Soft feel and drape
Wash and heat resistance
Excellent adhesion to polyester, nylon, spandex
Films are preferred over granules or powder in this industry for their ease of positioning, precise thickness, and clean lamination finish.
4.2. Automotive Industry
Applications include:
Bonding trim components
Headliners
Seat heating mats
Cable harnesses
Here, polyamide based hot melt adhesives are valued for their vibration resistance and long-term durability in high-temperature environments.
4.3. Electronics
Polyamide adhesives are widely used in:
Wire harness encapsulation
PCB bonding
Sensor and filter sealing
Their electrical insulation properties and chemical resistance make them a favorite in rugged electronics and industrial sensors.
4.4. Footwear & Leather Goods
These adhesives help bond synthetic leathers, linings, soles, and reinforcement fabrics. The flexibility and water resistance of polyamide hot melt adhesive films are vital in this area.
4.5. Technical Textiles
In filter media, outdoor gear, or industrial fabrics, polyamide based hot melt adhesive films offer excellent bonding with resistance to oil, high heat, and pressure.
5. Polyamide Hot Melt Adhesive Film: What Makes It Unique?
Hot melt adhesive films made from polyamide are thin sheets (generally 50–300 microns thick) designed for lamination between two substrate layers under heat and pressure.
Key Advantages of Film Form:
Precise Control: Thickness and shape are pre-defined.
Clean Processing: No mess, no overflow like melted granules.
Consistent Bonding: Uniform application ensures reliability.
Laser Cutting Friendly: Allows automated patterning in high-speed production.
Such films are commonly used in:
Lingerie lamination
RFID tag encapsulation
Embossed logos on technical apparel
Electronic insulation layers
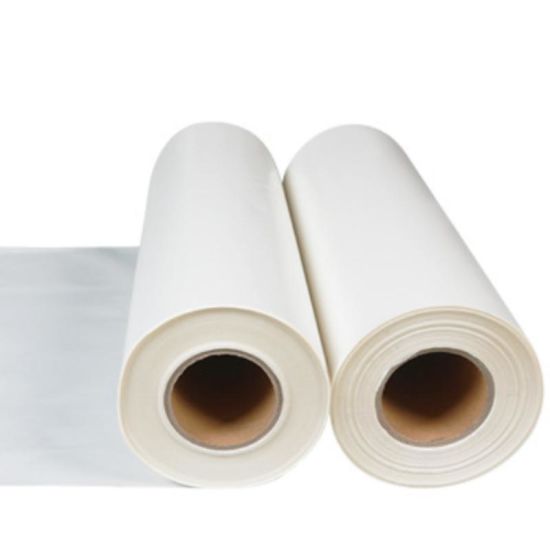
6. Processing Conditions for Polyamide Based Hot Melt Adhesive Film
To achieve optimal bonding, it’s important to match processing parameters to the specific film product:
Parameter | Typical Range |
---|---|
Melting Point | 100–160°C |
Pressing Temperature | 120–180°C |
Pressing Time | 10–30 seconds |
Pressure | 2–4 bar |
Cooling Time | 15–30 seconds under pressure |
Always test a small section before mass production, especially when working with sensitive fabrics or multilayer laminations.
7. Environmental and Safety Considerations
Polyamide based hot melt adhesives are generally considered eco-friendly compared to solvent-based glues:
No VOC Emissions: Safe for indoor use
No Toxic Byproducts: No formaldehyde or phthalates
Recyclable Waste: Solidified waste is non-hazardous
In addition, many film formats are REACH and OEKO-TEX certified, supporting compliance in textile and automotive exports.

8. Market Outlook and Trends
The global hot melt adhesive market is growing steadily, with polyamide based adhesives accounting for a rising share due to:
Surge in demand for technical textiles
Increase in wearable tech and flexible electronics
Shift toward seamless fashion and smart garments
Sustainability mandates in automotive manufacturing
Manufacturers and R&D labs are also developing bio-based polyamide adhesives to further reduce environmental impact, aiming to replace petroleum-derived materials in the coming decade.
Conclusion
In an industry landscape that demands performance, sustainability, and speed, polyamide based hot melt adhesives stand out as a versatile and high-value solution. Their superior bonding strength, heat and chemical resistance, and clean application make them an ideal choice across a wide range of applications.
Whether you’re in garment production, automotive assembly, electronics, or filtration, choosing the right polyamide hot melt adhesive, especially in film form, can lead to improved product performance and faster manufacturing cycles.
As more industries seek eco-conscious and high-performance bonding solutions, the role of polyamide based hot melt adhesives is only set to grow.