Ultrasonic sewing machines are an innovative solution in the textile and garment industries, offering a faster and more efficient way to bond fabrics. Unlike traditional sewing machines, which use needles and threads, ultrasonic sewing machines utilize high-frequency sound waves to create strong, seamless bonds between fabric layers. In this article, we will focus on the working principle behind this technology and explain how it operates to achieve these efficient results.
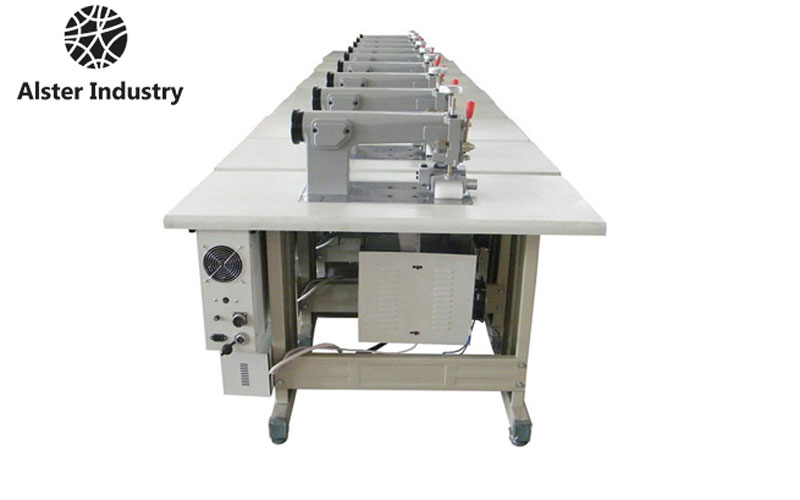
Introduction to Ultrasonic Sewing Machines
Ultrasonic sewing technology works by utilizing ultrasonic waves—sound waves with frequencies higher than the range of human hearing—to bond or weld materials. These sound waves are generated by a device called a piezoelectric transducer, which is capable of converting electrical energy into mechanical vibrations. The resulting vibrations are transmitted to the fabric through a horn, generating heat and pressure that melt and fuse the fabric layers together. This process eliminates the need for traditional stitching with needles and threads, making it a more efficient, environmentally friendly, and precise method.
The Key Components of Ultrasonic Sewing Machines
Several components work together to ensure that ultrasonic sewing machines operate smoothly and efficiently. Here’s a look at the key elements involved in the ultrasonic bonding process:
1. Piezoelectric Transducer
The piezoelectric transducer is the heart of the ultrasonic sewing machine. It plays a critical role in converting electrical energy into mechanical vibrations. This transducer is usually made from piezoelectric crystals that produce mechanical oscillations when an electrical current is applied to them. The ultrasonic generator supplies the transducer with high-frequency electrical signals, typically in the range of 20 kHz to 40 kHz.
When the electrical signals are transmitted to the piezoelectric crystals, they begin to vibrate at the ultrasonic frequency. These vibrations are the starting point for the bonding process. The transducer is responsible for converting the electrical energy into these mechanical vibrations, which are then used to bond fabric layers.
2. Horn or Welding Tool
The horn, also called a welding tool, is a component that amplifies the vibrations produced by the piezoelectric transducer. It is attached directly to the transducer, and its main purpose is to transmit the ultrasonic vibrations to the fabric layers that need to be bonded.
The horn is typically made of materials such as titanium or stainless steel, which are durable and capable of withstanding the intense vibrations. The shape of the horn is specially designed to focus the ultrasonic waves at the point where bonding is required. When the ultrasonic waves pass through the horn, they are directed to the fabric layers, causing them to vibrate and generate heat.
3. Vibration Transmission
Once the ultrasonic vibrations are produced by the transducer and transmitted to the horn, the vibrations are transferred to the fabric. The high-frequency vibrations create friction between the fibers of the fabric. This friction generates heat at the point of contact, causing the fabric’s fibers to melt. The melting temperature is usually low enough to fuse the fabric layers without damaging the surrounding area.
This process is highly localized, meaning that only the area where the ultrasonic waves are applied will experience heat. As a result, the rest of the fabric remains unaffected, preserving its integrity and structure. The controlled application of heat ensures that the fabrics are bonded precisely and cleanly without the need for excessive heating or unnecessary pressure.
4. Bonding Process: Fusion of Fabrics
The fabric layers are bonded together through the fusion of their fibers. The heat generated by the ultrasonic vibrations causes the fibers to melt at the point of contact, and as the material cools, it solidifies into a durable bond. This method of bonding creates strong, permanent seams that do not require any external stitching materials such as thread, glue, or adhesives.
The welding process occurs very quickly—often within a fraction of a second. This allows manufacturers, such as Alster, to achieve high production speeds without compromising the quality of the bond. The speed of the ultrasonic process makes it particularly attractive for industries that require large volumes of high-quality fabric bonding, such as in the textile, garment, automotive, medical, and packaging sectors.
5. Cooling and Solidification
After the ultrasonic energy has been applied and the fabric layers are fused, the next step is the cooling and solidification of the bond. This happens almost instantaneously once the ultrasonic waves stop. As the melted fabric cools, it solidifies, forming a strong, permanent bond.
The quick cooling process is one of the key advantages of ultrasonic bonding. Since it occurs so rapidly, it ensures that the production cycle is fast and that the bonded area does not remain soft or unstable for long. The bond created by ultrasonic welding is not only strong but also durable, often as strong or even stronger than traditional stitching methods.
Advantages of Ultrasonic Sewing Machines
Ultrasonic sewing technology offers numerous advantages over traditional sewing methods, making it an increasingly popular choice in various industries. Some of the most significant benefits include:
No Threading or Needles: Since ultrasonic machines do not require thread or needles, the process is significantly cleaner and more efficient. There’s no need to worry about thread breaks or needle wear.
Faster Production Speeds: The ultrasonic welding process is much faster than traditional stitching, which allows for higher production rates and improved efficiency.
Cleaner, Stronger Seams: The bond formed by ultrasonic waves is typically very clean and strong. There are no loose threads or frayed edges, which can often be a problem with traditional sewing methods.
Energy Efficiency: Ultrasonic sewing machines are typically more energy-efficient than traditional machines, as they consume only the necessary electrical energy to produce ultrasonic waves.
Environmentally Friendly: Without the need for threads or glue, ultrasonic sewing is an environmentally friendly process, producing less waste compared to conventional stitching methods.
No Need for External Materials: Because the fabric layers are bonded together without the use of additional materials, there is less reliance on external components like adhesives, which can sometimes cause contamination or lead to excess material waste.
Conclusion
The working principle of ultrasonic sewing machines revolves around the use of high-frequency sound waves to bond fabrics together. By employing a piezoelectric transducer to convert electrical energy into mechanical vibrations, the ultrasonic sewing machine generates heat and friction that cause the fabric fibers to melt and fuse. The process is fast, efficient, and highly precise, making it an excellent alternative to traditional sewing methods.
Ultrasonic sewing technology is not only faster and cleaner but also offers several advantages such as energy efficiency, strong bonds, and environmentally friendly operations. It is revolutionizing the way fabrics are joined in industries such as textile manufacturing, automotive, medical products, and packaging. As industries continue to seek faster and more cost-effective production methods, ultrasonic sewing machines will play an increasingly important role in shaping the future of textile and garment manufacturing.