In the world of modern garment manufacturing, precision and efficiency are key. As global demand for high-quality clothing continues to rise—especially for fashion-forward items like POLO shirts, suits, and formal shirts—textile factories must keep up with innovations that deliver consistent quality with minimal manual intervention. One of the most transformative technologies available today is the Ultrasonic Button Holes Punching Machine, specially engineered for creating clean, precise button holes on POLO shirts and other garments without damaging the fabric.
This blog post will explore the features, technical specifications, and key benefits of using ultrasonic button holes punching machine for POLO shirts. We’ll also explain how customizable molds and adjustable spacing provide unmatched flexibility for different fashion needs. Whether you’re a factory manager, garment producer, or textile equipment distributor, this guide offers deep insights into how ultrasonic buttonhole machines can streamline your production and enhance product quality.
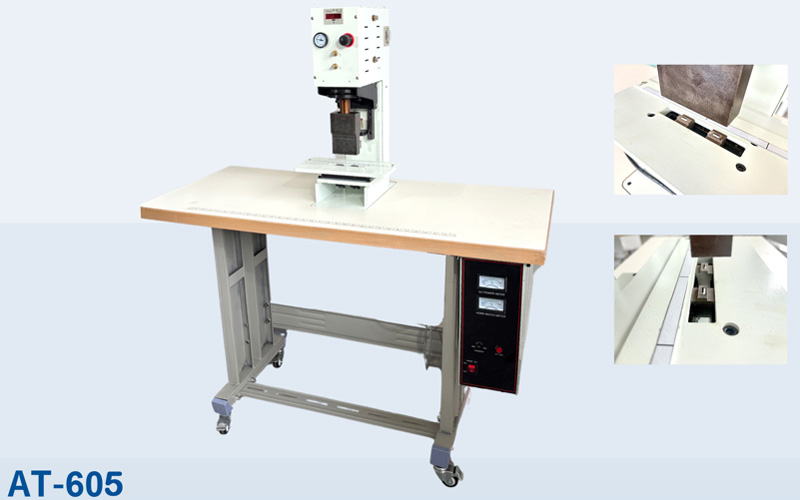
1. The Need for Advanced Button Hole Technology
Creating buttonholes might seem like a small task, but in professional tailoring and industrial garment production, buttonholes are a make-or-break detail. A poorly cut or scorched hole can ruin the look and quality of the garment. Traditional mechanical or laser-based punching methods often suffer from:
Frayed edges
Fabric scorching or blackening
Uneven cuts
Low durability in high-speed production environments
In contrast, ultrasonic cutting technology offers a non-contact, frictionless, and heat-controlled solution, making it ideal for modern fabrics like polyester, cotton blends, spandex, and other synthetics used in POLO shirts.
2. What Is an Ultrasonic Button Holes Punching Machine?
An Ultrasonic Button Holes Punching Machine uses high-frequency ultrasonic waves to generate localized heat through vibration. This vibration melts and fuses the fibers at the cutting point, resulting in a clean, sealed edge without burning or fraying.
The machine is specifically designed for garments like:
POLO shirts
Formal shirts
Jackets and suits
Uniforms and corporate wear
By combining ultrasonic cutting with pneumatic pressing, this machine delivers high-speed punching with flawless results—every time.
3. Key Features of the Ultrasonic Button Holes Punching Machine
Here are the standout features that make this machine essential for POLO shirt manufacturers:
· Seamless Buttonhole Cutting
The machine ensures that each cut is smooth, precise, and burr-free. There’s no scorching, no black marks, and no ragged edges. This is critical for white or light-colored shirts where even minor imperfections can be visible.
· Air Cylinder Driven Presser Foot
The pressing mechanism uses a pneumatic cylinder instead of mechanical parts, delivering stable pressure and reducing wear and tear on both fabric and machine components. This results in better control and uniform punching depth.
· Customizable Molds for Button Shapes
The machine supports custom mold design, which allows manufacturers to punch holes in different shapes and sizes based on garment requirements or designer preferences. You can also adjust hole spacing, making it highly adaptable for various clothing styles.
· Low Maintenance and High Efficiency
With fewer moving parts and an ultrasonic mechanism, the machine is less prone to mechanical failure and requires minimal maintenance. Its efficiency ensures that even high-volume production lines can maintain fast cycle times.
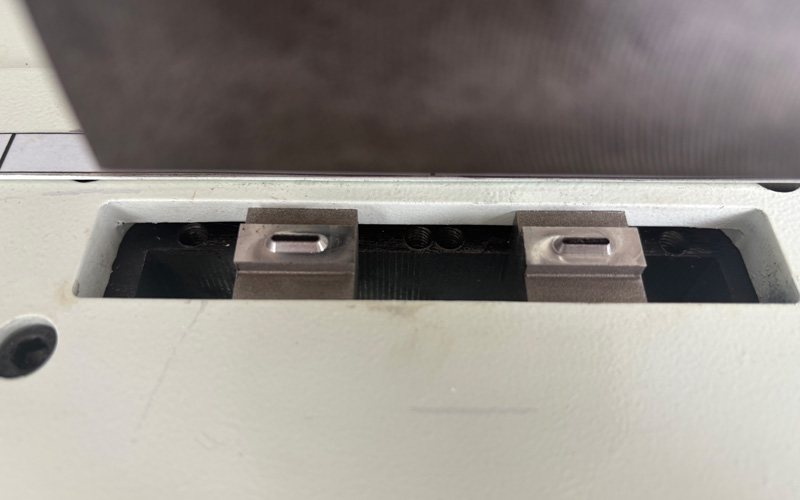
4. Technical Specifications
Specification | Description |
---|---|
Presser Foot | Air cylinder driven |
Maximum Power | 2800W |
Input Power | AC 220V, single-phase |
Compressed Air Pressure | 0.5 Mpa |
Ultrasonic Frequency | 18 KHz |
Net Weight | 130 kg |
Gross Weight | 190 kg |
Packing Size | 135 x 81 x 150 cm |
This configuration strikes an excellent balance between power output and precision control, ideal for mass production settings where uniform quality is essential.
5. Advantages of Ultrasonic Buttonhole Cutting for POLO Shirts
Let’s break down how this machine specifically benefits POLO shirt production:
· Maintains Fabric Integrity
POLO shirts are often made from cotton-spandex blends or polyester piqué, which can easily get distorted or frayed using traditional cutting methods. Ultrasonic cutting seals the edges instantly, preventing such damage.
· Consistency in Mass Production
Consistency is crucial when you’re producing thousands of garments daily. This machine ensures that every buttonhole is identical in size and shape, which boosts quality control and brand reputation.
· Speed and Throughput
Thanks to fast actuation and minimal downtime, production rates can significantly increase without compromising accuracy. High throughput is critical during peak fashion seasons or large contract orders.
· No Need for Post-Processing
Since the ultrasonic punch both cuts and seals the hole simultaneously, there’s no need for additional trimming or heat sealing, saving time and labor costs.
· Eco-Friendly Technology
Ultrasonic technology does not generate open flames or excessive heat, reducing energy consumption and environmental impact.
6. Customization Options: Molds and Spacing
One of the most attractive features of this ultrasonic punching machine is the ability to customize molds. Manufacturers can choose from:
Different buttonhole shapes (oval, round, rectangular)
Hole sizes for various button diameters
Adjustable distances between buttonholes
This flexibility supports the production of multiple clothing types with a single machine, eliminating the need to invest in several different units.
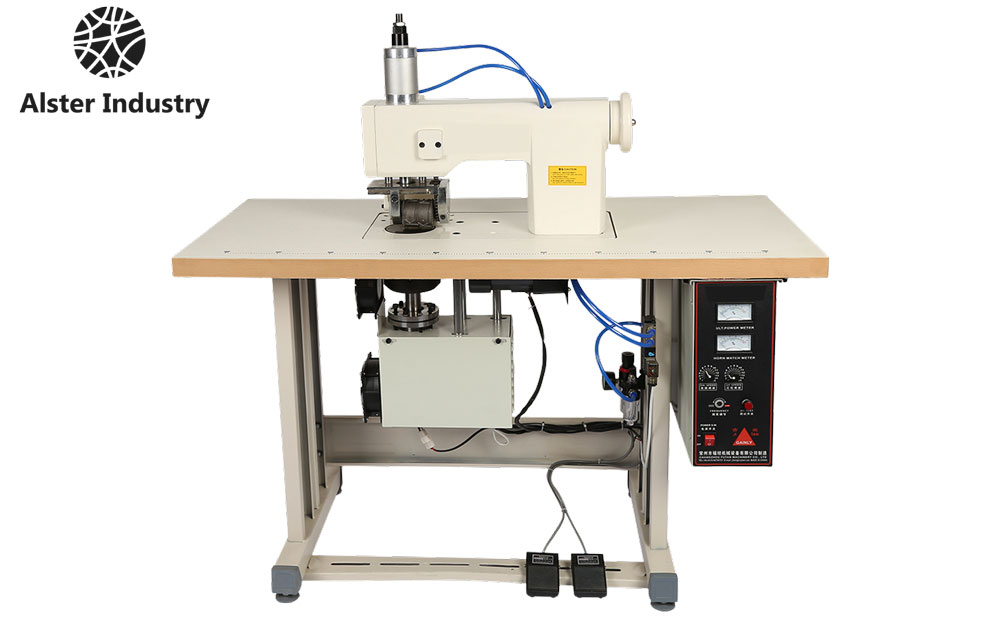
7. Common Applications Beyond POLO Shirts
Although designed with POLO shirts in mind, this ultrasonic machine is equally effective for:
Suits and formal wear (no fabric damage on delicate materials)
Shirts for uniforms (clean, identical cuts)
Children’s clothing (safe, sealed edges)
Fashion jackets and blouses
With adjustable pressure and mold options, the machine handles a variety of fabrics and sewing styles, making it a versatile tool for any garment factory.
8. User-Friendly Operation and Safety
· Intuitive Control Interface
Operators can easily adjust parameters such as pressure, frequency, and punch timing via digital controls. This minimizes training time and reduces the risk of user error.
· Safety Features
The machine includes:
Emergency stop buttons
Protective housings
Thermal overload sensors
These safety mechanisms ensure that the machine complies with factory safety standards and keeps operators safe.
9. How to Integrate This Machine into Your Production Line
Integration is straightforward. The compact size and moderate weight allow it to be:
Mounted as a standalone unit
Integrated with semi-automated shirt production lines
Paired with other ultrasonic or sewing machines
Additionally, standard 220V power and 0.5 Mpa air pressure requirements mean you likely already have the infrastructure needed to get started.
10. Maintenance Tips for Longevity
To ensure optimal performance, follow these maintenance guidelines:
Clean the ultrasonic horn regularly to prevent debris buildup.
Check pneumatic lines and seals for air leaks monthly.
Inspect the molds after every shift for wear or misalignment.
Lubricate moving components if necessary (excluding the ultrasonic system).
Run test punches before full-scale operation after long downtimes.
11. Why Choose This Ultrasonic Punching Machine Over Traditional Alternatives?
Feature | Ultrasonic Machine | Traditional Mechanical Punch |
---|---|---|
Cut Quality | Smooth, sealed, no burns | Frayed edges, possible scorching |
Speed | Fast and consistent | Slower, more manual intervention |
Maintenance | Low | Higher due to more moving parts |
Customization | High | Limited mold options |
Eco-Friendliness | High | Uses more energy or heat |
12. Ideal Buyers and Use Cases
This machine is highly recommended for:
Garment factories producing POLO shirts in bulk
OEM clothing manufacturers
Fashion brands offering customizable formal wear
Uniform manufacturers for schools, corporate clients, or military
Workwear and sportswear producers
Its versatility, safety, and quality output make it suitable for both small workshops and large-scale apparel production lines.
Conclusion: Boost Efficiency and Fabric Quality with Ultrasonic Technology
The Ultrasonic Button Holes Punching Machine is a game-changing solution for manufacturers aiming to produce high-quality POLO shirts and similar garments with precision and speed. By leveraging ultrasonic energy and pneumatic pressing, this machine delivers perfect buttonholes without damaging the fabric, all while reducing operational costs and labor time.
Add to that its customizable molds, eco-friendly operation, and user-friendly interface, and it’s clear this machine represents the future of garment manufacturing.
Interested in Learning More or Getting a Quote?
Whether you’re looking to upgrade your factory or seeking the best machine for a new product line, contact Alster today to:
Request a brochure
Schedule a demo
Inquire about mold customization
Get a quote with delivery options
Take your POLO shirt production to the next level with ultrasonic precision.