In the ever-evolving textile and apparel industry, efficiency, quality, and precision are key factors that determine competitiveness. One essential category of equipment that plays a pivotal role in achieving these qualities is the heat transfer printing machine. From high-volume industrial production to smaller-scale boutique manufacturing, these machines are indispensable in applying heat and pressure to bond materials together—whether for interlining fusing, label application, or creating decorative and functional finishes on fabric.
In this comprehensive guide, we’ll explore the types, functions, and applications of heat transfer printing machines, with a deep dive into two of the most advanced models in the market: the AT-F1200 Continuous Fusing Press Machine and the AT-6080 Flat Heat Press Machine. Whether you’re a factory owner, a production manager, or a procurement specialist, this guide will help you understand which solution best fits your operational needs.
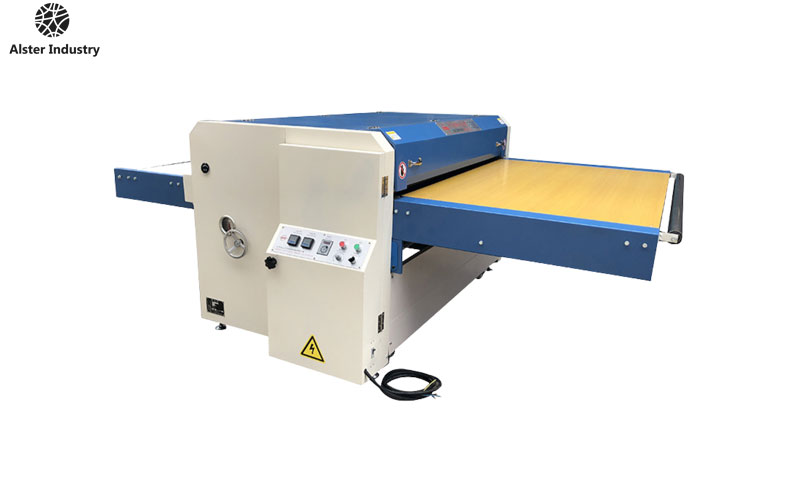
What Is a Heat Transfer Printing Machine?
A heat transfer printing machine is a device used to apply heat and pressure for a set period of time to transfer images, designs, or bonding agents onto various textile surfaces. These machines are widely used for:
Fusing interlinings in garments (especially in suits, shirts, and uniforms)
Printing graphics or labels onto apparel
Laminating high-performance or technical textiles
Creating seamless or wrinkle-free finishes in underwear and tops
Depending on the type of textile, scale of operation, and end-product quality requirements, different types of heat transfer machines are used.
How Does a Heat Transfer Printing Machine Work?
Most heat transfer printing machines operate on the principle of thermoplastic adhesion—using controlled heat, pressure, and dwell time to either transfer a layer (such as a vinyl print) or activate a fusible bonding agent (such as hot melt adhesive or interlining).
The core components include:
Heating elements (plates or rollers)
Pressure systems (manual, pneumatic, or hydraulic)
Timing and temperature controls
Conveyor or sliding platforms (for high-speed applications)
The accuracy of these parameters is crucial for consistent results, especially in mass production settings. Advanced machines feature programmable settings and sensor-driven controls to automate processes and reduce human error.
Main Categories of Heat Transfer Printing Machines
1. Flat Heat Press Machines
These are the most common types, consisting of a flat heated platen and a matching lower surface where the fabric is placed. The machine presses down for a set time and temperature to achieve bonding.
2. Roll-to-Roll or Continuous Fusing Machines
Designed for industrial applications, these machines use conveyor belts to continuously move fabric through heated rollers, making them ideal for fusing interlinings over long fabric lengths.
3. Pneumatic and Hydraulic Press Machines
Used where high pressure is needed for thicker or multi-layered fabrics. They provide more even pressure compared to manual presses.
4. Sublimation and Label Heat Transfer Machines
Specialized for transferring sublimation inks or pre-printed labels onto garments.
5. 3D Heat Press Machines
Used for printing on irregular or non-flat surfaces such as caps, shoes, or bags.
Featured Equipment: AT-F1200 Continuous Fusing Press Machine
For manufacturers looking to scale up operations and maintain high output with consistent quality, the AT-F1200 Continuous Fusing Press Machine stands out as an industrial-grade solution.
Key Features:
High-Speed Continuous Fusing: The conveyor-based system allows for uninterrupted operation, significantly improving productivity for medium to large-scale garment factories.
Wide Applicability: Ideal for fusing interlinings in suits, jackets, shirts, and sportswear, as well as technical and stretch fabrics.
Six-Zone Heating System: Ensures even heat distribution across the entire fusing surface, eliminating cold spots or overheating.
Silicone Pressure Rollers: Delivers stable and uniform pressure across different fabric types.
Mobility and Convenience: Equipped with wheels for easy movement and installation on the factory floor.
Smart Controls: PCB and micro switch systems automate belt movement, enhance safety, and prolong the life of the belt.
Applications:
Suit and Jacket Manufacturing
Uniform and Industrial Apparel
POLO and Dress Shirts
Seamless Sportswear
Stretch or Functional Textile Laminating
The AT-F1200 is the ideal heat transfer printing machine for high-volume fusing applications where speed and bonding strength are essential.
Featured Equipment: AT-6080 Flat Heat Press Machine
When it comes to ensuring wrinkle-free and smooth finishes for seamless underwear and upper garments, the AT-6080 Flat Heat Press Machine offers a powerful combination of precision, adaptability, and user-friendliness.
Key Features:
Thickened Reinforced Body: Ensures long-term durability and stability during continuous operation.
Dual Rail Sliders: Solve common alignment issues and improve the accuracy of pressing.
Semi-Automatic and Manual Modes: Operators can choose the preferred mode based on material type and batch size.
Adjustable Heating Plate Lift Speed: Prevents fabric damage and allows for customized processing.
Pneumatic Pressure Adjustment: Offers flexibility from 0 to 8kg/cm² to suit different textiles and finish requirements.
Digital Display: For time, temperature, and cycle count—enhancing control and productivity.
Applications:
Seamless Underwear
Women’s Panties
Fitted Tops
Lightweight and Stretchable Fabrics
Designed for both small batch and continuous production, the AT-6080 is a versatile heat transfer printing machine that elevates garment appearance while reducing manual labor and processing errors.
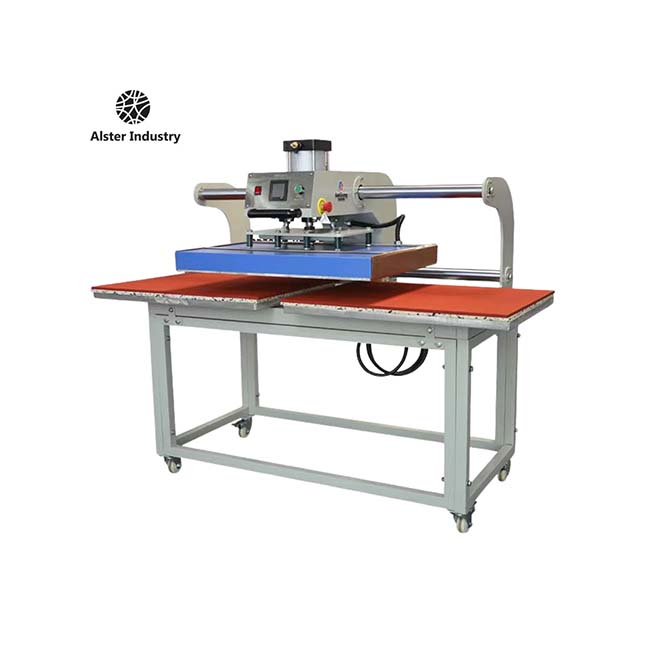
Key Considerations When Choosing a Heat Transfer Printing Machine
Production Volume
High-volume factories benefit from continuous machines like the AT-F1200, while small-scale manufacturers may find flat press machines like the AT-6080 more suitable.Fabric Type
Stretchable, technical, or delicate fabrics require precision in pressure and temperature. Machines with adjustable pneumatic settings are recommended.Space and Layout
Machines like the AT-F1200 need more space but offer higher throughput. Always consider the available space and workflow arrangement in your production facility.Automation Level
If minimizing labor is a goal, go for models with intelligent control systems, sensor-based automation, and programmable settings.Maintenance and Support
Choose manufacturers who offer global support, spare parts availability, and training—like those provided by Alster, the maker of AT-F1200 and AT-6080.
Benefits of Using Modern Heat Transfer Printing Machines
✅ Improved Bonding Durability
Consistent application of heat and pressure ensures stronger, longer-lasting bonding of interlinings or finishes.✅ Enhanced Productivity
Continuous models like the AT-F1200 drastically cut down processing times and increase daily output.✅ Higher Aesthetic Quality
Machines like the AT-6080 deliver wrinkle-free, smooth finishes that elevate product presentation and customer satisfaction.✅ Reduced Labor Costs
With semi-automatic and fully automatic options, you can reduce the number of skilled workers needed.✅ Energy Efficiency and Safety
New-generation machines feature smart systems that regulate energy usage and prevent overheating.
Why Alster’s Heat Transfer Printing Machines Stand Out
Alster is a trusted name in the textile machinery industry, known for its innovation, product quality, and after-sales service. Whether you’re upgrading an existing production line or building a new one, machines like the AT-F1200 and AT-6080 offer unmatched performance in their respective categories.
Alster offers:
- 📦 Professional installation and commissioning
- 🧑🏭 Operator training
- 🛠️ Long-term technical support
- 🚚 Fast spare parts delivery
- 🌍 Global service network
Conclusion
The right heat transfer printing machine can revolutionize your garment production—boosting speed, improving bonding strength, and reducing operational costs. Whether you need a high-speed fusing solution like the AT-F1200 Continuous Fusing Press Machine or a versatile hot press like the AT-6080 Flat Heat Press Machine, your choice should align with your specific production goals and fabric types.
Investing in reliable, feature-rich equipment from a reputable brand like Alster is not just a capital expense—it’s a long-term productivity strategy.
Ready to upgrade your garment production? Explore Alster’s full range of heat transfer solutions today.