In the world of modern intimate apparel manufacturing, seamless design is no longer a luxury—it’s a standard. One standout product that embodies this trend is the seamless silicone bra. These bras provide a smooth, invisible look under clothing while offering excellent comfort and support. The secret behind their flawless appearance and functionality lies in innovative manufacturing equipment, particularly the silicone brushing machine.
This article will guide you through the process of creating a high-quality seamless silicone bra using the silicone brushing machine, explaining each step and highlighting why this advanced technology is essential in the seamless garment industry.
What Is a Silicone Brushing Machine?
A silicone brushing machine is a specialized piece of equipment used in the production of seamless garments and lingerie, especially those involving silicone coatings. It allows manufacturers to apply precise and uniform layers of liquid silicone to fabric surfaces, forming stable, flexible, and invisible bonds or support structures. This machine ensures the coating adheres accurately to the desired area without bleeding, distortion, or rough edges—critical qualities for items like seamless bras.
At Alster Industry, we provide top-tier silicone brushing machines integrated with bonding technology and hot melt adhesive tape systems to support high-end production for brands and OEMs worldwide.
Materials Required to Make a Seamless Silicone Bra
Before diving into the process, let’s look at the essential materials:
Fabric: Stretchable, breathable fabrics such as nylon-spandex blends or modal
Liquid Silicone: High-quality, medical-grade or clothing-grade silicone
Hot Melt Adhesive Tape: For bonding layers without stitching
Bra Mold or Pressing Equipment: To shape the cups and body
Silicone Brushing Machine: For applying liquid silicone precisely
Heat Press Machine or Ultrasonic Sealing Machine: Optional, for fusing non-silicone parts
Step-by-Step Process Using a Silicone Brushing Machine
Step 1: Design and Pattern Cutting
First, the bra’s design is created using CAD software, and patterns are cut from stretch fabric. For a seamless look, fabric edges are kept raw and clean. The target areas for silicone application (e.g., under-bust support, side wing reinforcements, or cup perimeters) are marked accordingly.
Step 2: Preparing the Silicone Brushing Machine
The silicone brushing machine must be prepped by loading it with the correct type and viscosity of liquid silicone. Depending on the application, the brush width, stroke speed, and curing temperature settings may need adjustments. For seamless silicone bras, precision and cleanliness are vital—Alster Industry’s machines offer high-speed, programmable controls for ultimate accuracy.
Key Benefits of the Silicone Brushing Machine:
Accurate silicone line thickness control
Automated silicone placement via program templates
Clean edges without overflow
Fast curing and low material waste
This ensures the silicone stays exactly where needed, without affecting the soft touch and stretch of the surrounding fabric.
Step 3: Silicone Application
Once configured, the silicone brushing machine starts applying silicone to designated zones on the bra fabric. For instance, a thin layer around the edge of the cups adds grip and helps the bra hold its shape. Silicone can also be brushed in curved patterns beneath the cups for invisible support or anti-slip functions.
Silicone bonding eliminates the need for elastic bands or underwires, resulting in a more comfortable wearing experience. Additionally, silicone areas can be customized in width and texture to meet different market demands, such as yoga bras, maternity wear, or everyday seamless intimates.
Step 4: Silicone Curing
Most silicone brushing machines include a built-in curing unit that applies low-level heat or UV exposure to fix the silicone instantly. Depending on the formulation, the silicone may cure at 100–150°C in just seconds, allowing for high-speed mass production.
If using a separate curing tunnel or oven, the bras are transferred and heated gently to solidify the silicone without affecting fabric elasticity.
Step 5: Assembly and Bonding
After silicone application, the bra components (cups, wings, straps) are bonded together using hot melt adhesive tapes. This stitch-free method preserves the seamless look and feel. At Alster Industry, we supply advanced hot melt adhesive films and tapes specifically designed for lingerie, offering excellent bonding strength with minimal thickness.
An additional heat press or ultrasonic welding step may be used to permanently bond overlapping fabrics or attach logos and labels.
Step 6: Final Shaping and Inspection
The nearly finished bra is placed into a mold to form the final contour shape. A quick heat press locks in the curvature and seamless design. After cooling, the product is inspected for uniformity, silicone accuracy, and overall quality.
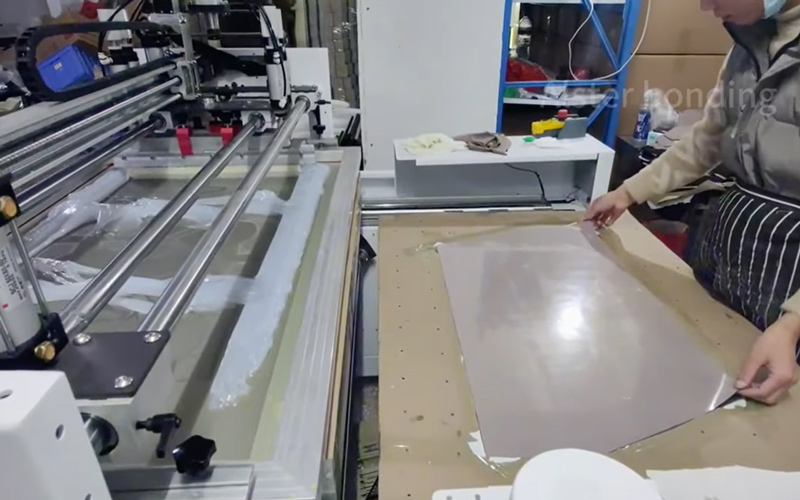
Why Use the Silicone Brushing Machine for Seamless Bras?
Using a silicone brushing machine offers several advantages in seamless bra production:
Consistency: Every product receives the exact same amount and shape of silicone.
Efficiency: Automated systems reduce labor time and errors.
Clean Finish: No messy edges or irregular lines—essential for visible innerwear.
Custom Patterns: Programmable application allows manufacturers to create complex or brand-specific silicone designs.
Material Compatibility: Works with a variety of fabrics including mesh, microfiber, Lycra, and lace.
Whether you’re a start-up in the lingerie market or an established brand expanding into seamless solutions, integrating a silicone brushing machine into your production line can elevate your product quality significantly.
Maintenance and Operation Tips
To get the best performance from your silicone brushing machine, follow these operational tips:
Clean the brush heads regularly to avoid clogging.
Use only compatible liquid silicone for your specific machine.
Calibrate the brushing paths according to fabric stretch rate.
Train operators on precise parameter settings to prevent silicone wastage.
Alster Industry provides comprehensive machine manuals and technical support to ensure your team operates at maximum efficiency.
Seamless Bra Trends & Market Potential
Seamless bras are in high demand, especially post-pandemic, as consumers seek comfort without compromising style. Athleisure, maternity, and invisible undergarments all benefit from silicone support systems. Brands looking to gain a competitive edge must embrace clean technology and faster production solutions.
The silicone brushing machine, paired with bonding machinery and hot melt adhesive tapes, is not just a tool—it’s a gateway to innovation in the apparel industry.
Conclusion
Creating a seamless silicone bra is a detailed yet rewarding process. With the help of a high-precision silicone brushing machine, manufacturers can achieve the perfect blend of support, comfort, and aesthetics. Whether you’re entering the seamless market or upgrading your current production line, this technology is a must-have for future-ready apparel factories.
Looking to upgrade your garment production line with cutting-edge bonding technology?
At Alster Industry, we specialize in silicone brushing machines, bonding machinery, and hot melt adhesive film for seamless garment manufacturing.
🌐 Visit our website: www.alsterindustry.com
📞 Whatsapp/Wechat: +86 17621495137
📧 Email: info@alsterindustry.com
We’re here to support your innovation—contact us today for more information or to request a quote!