In the era of high-precision manufacturing and functional aesthetics, the seamless bonding machine has emerged as a key enabler of quality and innovation. The machine is no longer a novelty—it has become an industrial standard in sectors where fabric quality, wearability, hygiene, and durability are non-negotiable. Below, we will examine in depth the advantages of seamless bonding machines, specifically from the perspective of production efficiency, product quality, user comfort, sustainability, and market competitiveness.
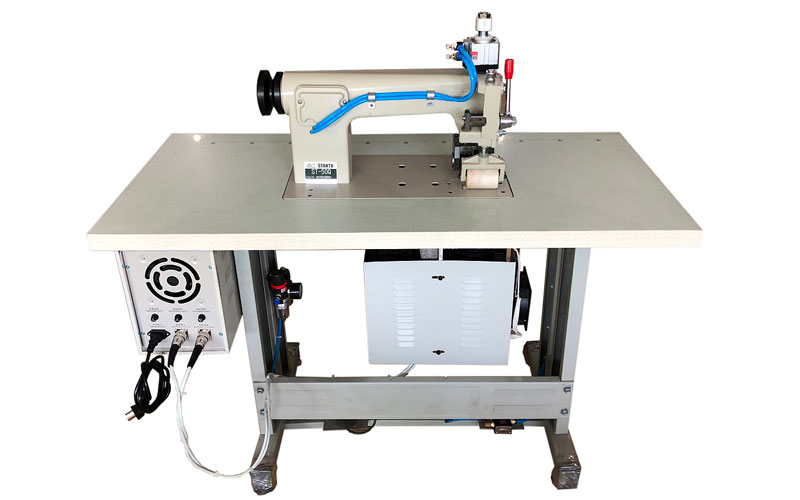
1. Enhanced Wearing Comfort for End Users
Seamless bonding creates garments and materials with a soft, smooth interior, free from raised seams or overlapping stitching. This offers unparalleled wearing comfort, especially for applications involving direct contact with the skin.
No abrasive stitches: Traditional seams often chafe against the skin, especially in high-friction areas like underarms, thighs, or necklines. Bonded seams remove this discomfort.
Ideal for sensitive skin: Lingerie, underwear, babywear, and medical garments benefit immensely from a construction that reduces irritation.
Perfect for extended wear: Athletes, travelers, or patients wearing garments for long durations experience enhanced comfort without hot spots or skin indentations caused by pressure seams.
2. Aesthetic Superiority and Premium Appearance
The visual appeal of products made with seamless bonding technology is unmistakable. The absence of stitching lends a cleaner, more modern look to garments, accessories, or industrial components.
Clean lines: Smooth, minimalist design lines enhance visual uniformity.
Invisible seams: Bonded edges are virtually unnoticeable, giving the product a premium and futuristic finish.
Ideal for performance wear: Sports and activewear benefit from aesthetic and functional synergy—no bulk, no lines, just performance.
High-end product positioning: The flawless appearance of bonded garments adds a luxury feel, helping brands position their products as top-tier.
3. Exceptional Strength and Durability
While some assume bonded seams may be weaker, the opposite is true when the bonding process is executed correctly.
Uniform pressure: Seamless bonding applies consistent thermal or ultrasonic pressure across the joint, which minimizes weak points.
Long-lasting adhesion: The bonded areas typically endure repeated wash cycles, stretching, and environmental exposure without fraying or loosening.
No stitch holes: The removal of needle punctures increases seam integrity and prevents weakening over time.
From outdoor jackets to safety gear, products made with bonding technology are better equipped for wear and tear.
4. Functional Benefits: Waterproof, Windproof, and Air-Sealed
Bonded seams eliminate the needle holes associated with conventional sewing. This is vital in applications where maintaining a barrier is essential.
True waterproofing: Rainwear, ski suits, wetsuits, and military uniforms demand a full seal to keep moisture out.
Wind resistance: A continuous bond ensures no air gaps for cold drafts to enter, improving thermal performance.
Dust and fluid barrier: Medical and industrial applications rely on bonded seams to reduce contamination risk.
These benefits extend into numerous industries including outdoor gear, technical apparel, healthcare, and aerospace.
5. Reduction in Production Time and Operational Efficiency
Seamless bonding machines often automate what used to be a multi-step, manual process. This leads to measurable improvements in productivity.
Single-pass operation: Bonding can often be done in one continuous motion, compared to stitch-by-stitch sewing.
No need for thread changing or tension adjustments.
Quicker training cycles: Operators can learn machine settings and adjustments faster than mastering manual sewing skills.
Fewer production line errors: Less manual intervention means fewer human errors and less need for quality control rework.
Manufacturers benefit from faster order fulfillment and improved production planning.
6. Compatibility with Complex and Technical Fabrics
As new textiles are developed—especially synthetic and blended fabrics with functional properties—traditional sewing struggles to maintain integrity and aesthetics.
No material distortion: Bonding applies heat and pressure instead of penetrating the fabric, preserving its shape and elasticity.
Works with stretch fabrics: Seamless technology is ideal for Lycra, elastane, neoprene, and other performance materials.
No skipped stitches: Stitch skipping is common in certain fabrics due to inconsistent friction. Bonding avoids this entirely.
This advantage makes the technology particularly valuable for manufacturers of activewear, shapewear, compression garments, and medical-grade textiles.
7. Lightweight Product Outcomes
Garments made with seamless bonding technology are inherently lighter due to the absence of thread and overlapping fabric.
Better for performance: Reduced weight supports athletes and outdoor users who rely on lightweight gear.
Optimized for packing: Slimmer seams allow for better compression and folding.
Efficient layering: In fashion and industrial applications, thinner construction supports multi-layer use without bulk.
This is particularly helpful for travelers, military personnel, and professionals using technical clothing in extreme conditions.
8. Fewer Consumables and Reduced Material Waste
Seamless bonding machines operate without thread, bobbins, and many of the consumables required in conventional sewing. This leads to:
Less inventory required: No need to stock dozens of thread colors and types.
Lower material wastage: Bonding processes can be more precise, reducing trimming waste and sewing rejections.
Reduced production cost: Long-term savings from fewer consumables and better yield rates.
Over time, these cost reductions significantly impact the bottom line for manufacturers.
9. Eco-Friendly Manufacturing Process
Environmental impact is a growing concern in the textile industry. Seamless bonding machines contribute positively to sustainability goals.
No microplastic release from thread degradation.
Less water usage: Seamless production lines often integrate dry processes that require no water for seam finishing or washing.
Compatibility with recyclable adhesives: Some hot-melt films used in bonding are recyclable or biodegradable.
Longer-lasting products: Increased garment durability reduces the frequency of replacement and landfill contribution.
These advantages help brands align with ESG initiatives and improve their public image as responsible producers.
10. Labor Efficiency and Reduced Workforce Dependency
As global labor shortages and rising wage costs affect garment industries, seamless bonding offers a solution.
Automation-friendly: Machines can be integrated into robotic lines or CNC-guided processes.
Lower training requirements: Compared to traditional sewing machines, bonding systems can be operated with minimal manual skill.
Stable output: With fewer human variables, production becomes more predictable and consistent.
This is particularly beneficial for high-wage markets or regions transitioning from low-cost manufacturing to automation-driven production.
11. Customization and Modular Integration
Seamless bonding systems are highly adaptable and can be configured to meet specific production needs.
Adjustable settings: Temperature, pressure, and bonding time can be modified to suit different materials.
Modular add-ons: Machines can be fitted with cutters, rollers, cooling stations, or adhesive applicators depending on the workflow.
Inline integration: Bonding machines can be placed in-line with fabric printing, cutting, and inspection stations.
This flexibility supports both mass production and small-batch custom projects.
12. Strong Market Differentiation for Brands
In a saturated apparel market, offering seamless products can elevate a brand above competitors.
Perceived quality: Seamless garments are widely viewed as more sophisticated and innovative.
Visual uniqueness: Clean silhouettes stand out on shelves and in promotional materials.
Storytelling value: Brands can leverage seamless technology as part of their sustainability or innovation narratives.
This differentiation drives consumer loyalty and premium pricing power.
13. Improved Hygiene and Sterility in Specialized Applications
For medical, healthcare, and food-service industries, seam cleanliness is critical.
No bacteria accumulation: Traditional seams can trap dirt and microbes. Bonded seams are easier to sterilize and clean.
Smooth surfaces: This minimizes risk in surgical environments or sterile production zones.
No broken threads: Frayed stitches can compromise hygienic barriers. Seamless bonding avoids this entirely.
This opens up critical uses in disposable PPE, surgical wear, and hygienic packaging solutions.
14. Excellent Results in Combination with Hot Melt Adhesives
When used with high-performance adhesive films, seamless bonding machines achieve optimal strength and flexibility.
Elastic bonding: Suitable for sportswear or active gear that needs to stretch without tearing.
Thermoplastic compatibility: Wide range of adhesive types available for different applications.
Controlled bonding temperature: Ensures no burning or damage to delicate materials.
The pairing of bonding machines with advanced adhesives allows manufacturers to fine-tune products based on performance requirements.
15. Reduced Post-Processing Requirements
Conventional sewing often involves multiple post-processing steps—trimming, serging, finishing edges, and pressing. Bonded seams often require none.
Fewer steps: Heat and pressure bonding results in already-finished seams.
No edge fraying: Eliminates the need for additional sealing or binding.
Time savings: Products are closer to “ready to pack” after bonding.
This simplifies the supply chain and shortens lead times from factory to customer.
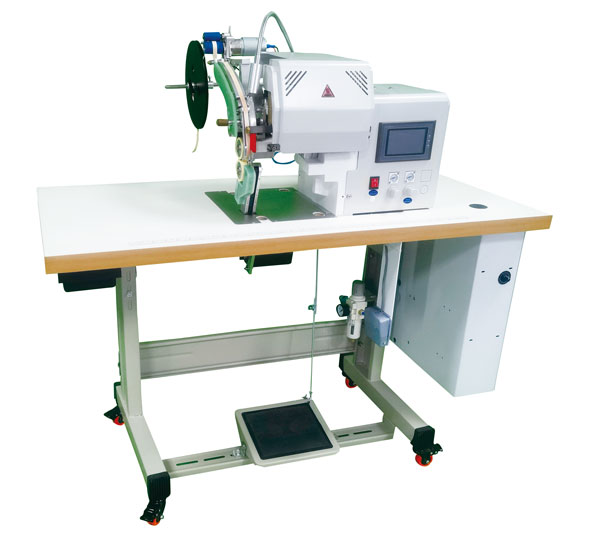
Conclusion: A Competitive Must-Have for the Modern Manufacturer
The advantages of seamless bonding machines span virtually every major concern of the modern manufacturing operation—comfort, appearance, strength, efficiency, sustainability, and differentiation. These machines are not just tools—they are long-term assets that enable manufacturers to meet changing consumer demands, stricter quality standards, and tighter production schedules.
From the workshop floor to the retail shelf, the transition to seamless bonding represents a forward-looking investment in product innovation and operational excellence.
If you’re seeking to streamline production, reduce costs, and deliver world-class quality, seamless bonding machines offer a compelling strategic advantage that is hard to ignore. More about these kinds of seamless bonding machine, welcome to contact Alster – professional bonding machine and adhesive film manufacturer in China!